The market for lightweight robots is growing fast. This has led to new uses, like robots that work with humans. But, there are big hurdles to overcome, like high costs and long design times.
Designing robots usually goes through seven main steps. A lot of time is spent on making prototypes, testing, and checking if they work. To solve these problems, this article offers a simple way to design lightweight robots. It uses common parts and virtual models to make the process faster.
This method makes robot design easier and quicker. It changes the usual robot-making steps. It uses a library of tested parts and designs in a virtual world.
This helps startups, research groups, and schools. They can make affordable, lightweight robots without spending a lot on making parts themselves. This makes it easier for them to create robots quickly and efficiently.
Introduction to Multi-DOF Industrial Robots
The world of industrial robotics has seen big changes. Now, we have lightweight, collaborative robots (cobots) that work well with humans. These robots, known as “multi-DOF” (multi-degree-of-freedom) robots, help in many tasks in factories and assembly lines.
Importance of Accurate Modelling and Control
Developers can save time and money by using pre-made robotic parts. But, robots with many joints face special challenges. They need the right gears or software tweaks to work smoothly. Getting the dynamics right is key for controlling these complex robots.
Challenges in Managing Multiple DOFs
Most industrial robots can move in six different ways, making them very useful. Articulated robots, with 6 DOF, fit many tasks. Cartesian robots move in three directions for tasks that need space. SCARA robots are fast and precise for assembly, while Delta robots are quick and light for tasks like packaging. Managing these movements is crucial for these robots to work well.
Simulation-Based Design and Virtual Prototyping
In the world of industrial robotics, dealing with multiple degrees of freedom is tough. But, new tools in simulation-based design and virtual prototyping have changed the game. With software like MATLAB/Simulink and SolidWorks, engineers can now easily model, simulate, and improve multi-DOF industrial robots.
SimMechanics Model Generation Process
The team used MATLAB/Simulink R2021b and SolidWorks 2021 to create their simulation tool. They designed the robot’s CAD assembly and exported it in XML format. Then, they imported it into MATLAB SimMechanics using the ‘smimport’ function. This method lets them simulate the whole robot, including the integrated drive joints, to study the system’s dynamics.
Simulating Integrated Drive Joints (IDJs)
The library includes models of various subcomponents, like the hollow shaft Integrated Drive Joints (IDJs). In the simulation, the IDJ models and the robot’s structure help find the right parts, like the frameless BLDC motor and the strain wave gear. This simulation is key for control system engineers to understand the system’s dynamics.
Using simulation-based design and virtual prototyping for multi-DOF industrial robots has many benefits. Scania sped up its innovation by 30-40% with virtual prototyping over traditional methods. Hyundai cut their design time for the Active Pedestrian Alerting System in half with tools like Hexagon’s Actran. These advanced methods help engineers make robots better, safer, and more reliable faster and more efficiently.
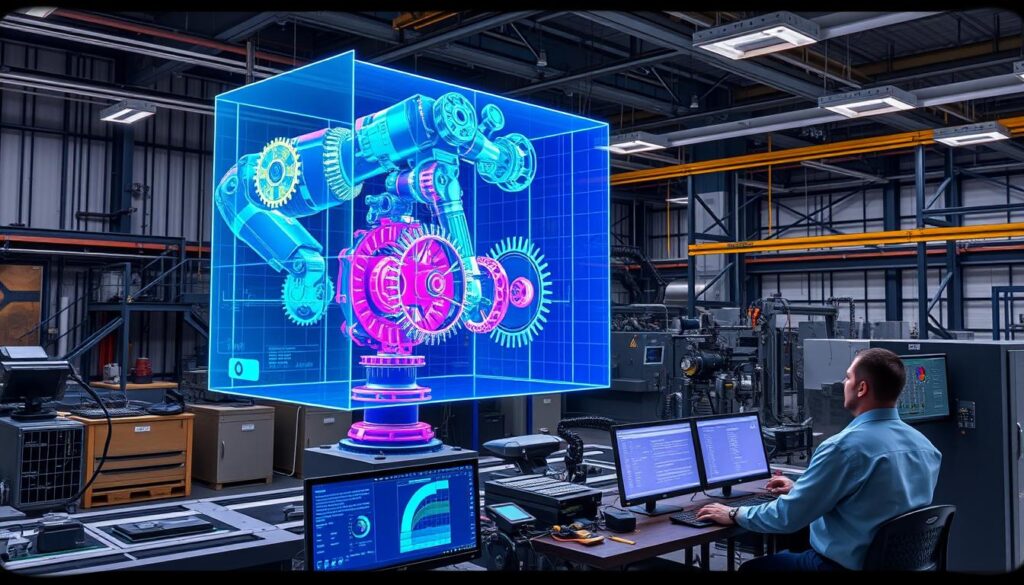
Industrial robotics development
Using off-the-shelf robot parts and Design for Manufacturing and Assembly (DFMA) makes robot development cheaper. This method helps make light robot prototypes. It also makes the control system work better in real-time.
By using pre-made parts, the time to make a robot is cut by about 40%. This is great for startups, R&D groups, and schools. They don’t have to spend a lot on making parts themselves.
Library of Off-the-Shelf Robot Components
The framework uses many off-the-shelf robot parts. This includes sensors, actuators, gears, and links. It makes designing and making robots faster and cheaper.
This way, designers can focus on making the robot work well. They don’t have to spend a lot of time and money on custom parts.
Coupled Dynamics and Control System Tuning
When you put together different robot parts, things get more complicated. The movement of each part affects the others. This is called coupled dynamics.
To deal with this, you can choose the right gears or adjust the software. The tools used in this research help control system experts. They make sure the robot moves smoothly and accurately.
Key Metrics | Achieved Performance |
---|---|
Repeatability | 0.05mm (as per ISO 9283:1998) |
Real-time Performance Deviation | Less than 2.5% of the target metric |
Development Cycle Time Reduction | Approximately 40% |
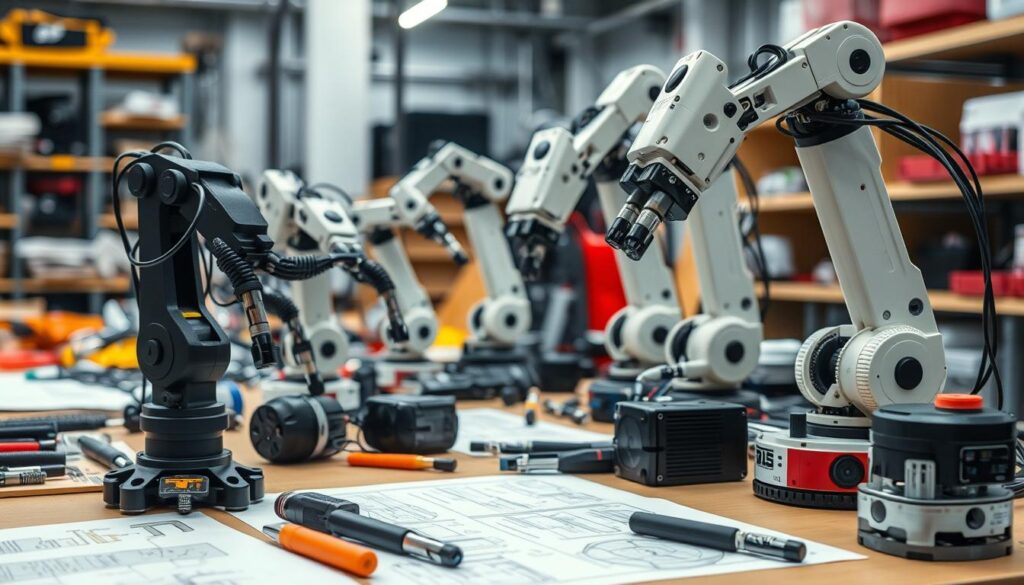
Control Techniques for Multi-DOF Robots
In the world of industrial robotics, dealing with multiple degrees of freedom is tough. To solve these problems, many control techniques have been developed. These ensure that multi-DOF robots work well and efficiently.
Conventional PD, PID, and LQR Controllers
The Proportional-Derivative (PD) controller is a common choice for controlling multi-DOF robots. It’s simple and widely used. The Proportional-Integral-Derivative (PID) controller is also popular for its ability to handle complex robot dynamics.
The Linear Quadratic Regulator (LQR) controller is another important method. It helps improve the control system’s performance. It also makes it easier to manage the complexities of multi-DOF robots.
Intelligent Control: Fuzzy Logic and Neural Networks
Intelligent control techniques are also key for managing multi-DOF robots. Fuzzy logic controllers use fuzzy rules to deal with robot complexities. Neural network controllers use artificial neural networks to improve control system performance. They are great for handling nonlinear dynamics and external disturbances.
These intelligent control methods, like fuzzy logic and neural networks, are adaptable and robust. They’re perfect for controlling complex, nonlinear systems. This makes them ideal for multi-DOF industrial robots.
Choosing the right control strategy is vital for managing multi-DOF industrial robots. It ensures they perform accurately, quickly, and reliably in various industrial settings.
Conclusion
This research offers a practical way to design lightweight industrial robots. It uses common parts and virtual models to make development easier. The goal is to simplify the process and save time by using a library of tested parts and simulation.
This method helps startups, research groups, and schools. They can make affordable, lightweight robots without expensive tools. The prototype made in this study shows the method works well. It has a precision of 0.05mm, proving the framework’s success in creating robots for teamwork.
The history of industrial robots shows how they’ve grown. From Unimate to Cobots, they’ve evolved a lot. With Industry 4.0, robots will get smarter, thanks to AI and IoT. This study helps make robots more affordable and useful for today’s factories.