Industrial robotics combines many techniques to boost robot performance in factories. These include optimizing tasks, programming offline, and using sensors. Engineers also focus on planning paths, avoiding collisions, and using smart algorithms.
Robots with machine vision and AI can work better and safer. They use less energy and perform better. Adding end-effectors and collaborative robots makes them even more versatile.
Thanks to these advanced methods, engineers can make robots work faster and more efficiently. This helps in making new products quicker. It also lets robots work together without any problems.
Introduction to Path Planning in Industrial Robotics
Path planning is key for robot intelligence. It helps industrial robots move through complex spaces without crashing. With the rise of smart factories, making sure robots move safely and efficiently is more important than ever.
Significance of Path Planning in Robot Intelligence
Path planning uses vision tech to find out where objects are. It tells robots the best way to move and how to use each joint. This makes sure they can do their jobs well.
Applications of Industrial Robots in Manufacturing
Industrial robots are used in many factory tasks like welding and assembly. They are part of a big market that’s growing fast. In 2022, the robotics market is expected to hit $51.3 billion, with robots making up $19.5 billion of that.
Even though robots are still developing, they face challenges like needing manual fixes and safety issues. But, robotics is getting more attention. Path planning is crucial for robots to work safely and well.
Characteristics of Path Planning for Industrial Robots
Path planning for industrial robots is complex due to their high-dimensional spaces. They need to plan collision-free paths to work efficiently. This involves looking at planning dimensions, collision detection, and using vision and sensing technologies.
Path planning is crucial for industrial robots. It affects safety, time, and cost savings. It also reduces wear and tear on the robot. Traditional robots are used in dangerous or hard-to-reach places.
Mobile manipulators mix a robotic arm with a mobile base. They’re used in logistics and manufacturing. Advanced sensors like 3D cameras and LiDAR help them navigate better.
Path planning algorithms for mobile manipulators are getting better. They help find the best routes and avoid obstacles. This makes navigation safer and more efficient.
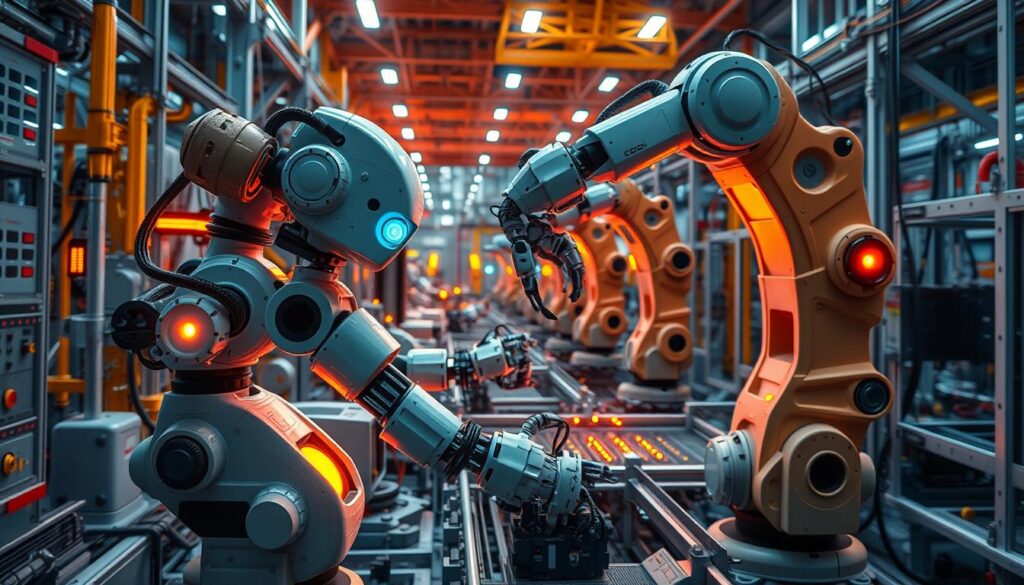
Robot manipulators are great at handling different objects with precision. They can adapt to various tasks with improved sensory perception. This makes them flexible and accurate.
Mobile manipulation robots help in logistics and healthcare. They automate tasks like material transport and quality control. Their versatility and safety features are making them more popular.
Industrial robotics development: Rapidly-Exploring Random Tree (RRT) Algorithm
The Rapidly-Exploring Random Tree (RRT) algorithm is a key tool for path planning in industrial robotics. It’s known for its skill in exploring complex spaces. This is vital for robots to move around safely and efficiently.
Sampling Techniques in RRT Algorithm
Sampling techniques are crucial for the RRT algorithm’s success. Researchers have looked into different methods to make the algorithm smarter and faster. They aim to help robots find the best paths without hitting anything.
Connection Measurements for RRT Algorithm
The connection step in the RRT algorithm is important. It decides how points are linked together. By studying different ways to connect points, experts hope to make the algorithm better at finding paths for robots.
Metric | Description | Impact on RRT Algorithm |
---|---|---|
Euclidean Distance | Measures the straight-line distance between two points in the high-dimensional space. | Simplistic, but may not accurately capture the complexity of industrial robot movements. |
Kinematic-based Distance | Considers the robot’s joint angles and link lengths to calculate a more realistic distance metric. | Provides a better representation of the robot’s physical constraints, improving path planning accuracy. |
Visibility-based Distance | Evaluates the visibility between sampled points, accounting for obstacles and workspace constraints. | Enhances the algorithm’s ability to navigate cluttered industrial environments, reducing the risk of collisions. |
The choice of connection measurement technique is key for the RRT algorithm’s success. Experts keep looking for new ways to improve it. They want to make the algorithm even better at guiding robots through complex spaces.
Collision Detection and Path Query in RRT Algorithm
In the world of industrial robotics, the Rapidly-Exploring Random Tree (RRT) algorithm is key. It helps plan paths and optimize trajectories. It’s important for avoiding collisions and finding the best path for robots.
Experts are working hard to make these processes better. They use advanced methods to improve the RRT algorithm. These methods help robots move safely and find the shortest path.
- Path planning is important in many areas like robotics and manufacturing.
- Algorithms like RRT and PRM help plan paths for robots.
- RRT-Connect is a special version of RRT for efficient path planning.
Researchers have been studying how to make the RRT algorithm better. They’ve come up with new ideas like goal-oriented sampling. These ideas help robots move more efficiently and safely in complex environments.
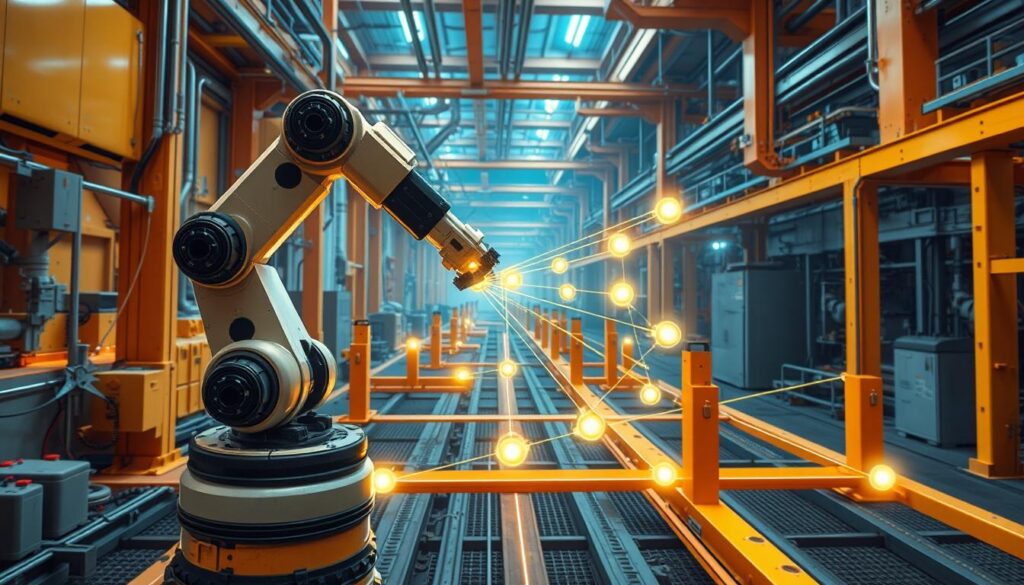
The need for better industrial robots is growing. Improving the RRT algorithm’s collision detection and path query is key. Researchers are always looking for new ways to solve these challenges, making robots more reliable and efficient.
Challenges and Future Trends in RRT-based Path Planning
Industrial robots are crucial in today’s manufacturing. Yet, using the Rapidly-Exploring Random Tree (RRT) algorithm poses challenges. One major issue is avoiding obstacles in real-time.
Robots work in complex, ever-changing settings. They need to plan paths that can adjust to obstacles instantly. This ensures safety and efficiency. Researchers are looking into using sensors and vision systems to help robots detect and avoid obstacles.
Real-time Obstacle Avoidance Path Planning
Using vision and sensing technologies with RRT is a big trend in robotics. Advanced sensors and vision systems help robots understand their surroundings better. This lets them plan more precise paths.
This is key for intelligent manufacturing. Robots must work well with humans and adapt to changing environments.
Integration with Vision and Sensing Technologies
Researchers are working to make RRT better for dynamic environments. They’re exploring artificial potential fields, informed sampling, and path optimization. These methods aim to improve navigation, reduce costs, and create smoother paths.
The need for flexible, smart manufacturing systems is growing. Integrating advanced algorithms like RRT with vision and sensing technologies is a major focus. Researchers and engineers are working hard in this area.
Conclusion
Path planning and trajectory optimization have greatly improved industrial robots. Engineers use advanced algorithms like the Rapidly-Exploring Random Tree (RRT) algorithm. This makes robots more efficient and precise, allowing them to handle complex tasks.
The global robotics market is growing fast. Path planning and trajectory optimization are key to smart factories and intelligent manufacturing. Researchers are working on vision and sensing technologies to make robots smarter and more adaptable.
Industrial robotics is evolving from Industry 2.0 to Industry 4.0. This change brings new technologies like collaborative robots (cobots) and humanoid robots. These innovations will help robots work better with humans, making manufacturing more efficient and collaborative.