Integrating industrial robots with cloud-based systems is key in industrial robotics development. It boosts productivity and makes troubleshooting easier. It also improves control over robotic systems engineering.
Cloud-based tech lets manufacturers check and manage their robotic systems from afar. This cuts down on the need for on-site workers and reduces downtime. It also helps solve robot problems quickly, saving costs and improving industrial automation solutions.
The use of automation technologies in industrial robotics is growing fast. This is because businesses want to automate more in different fields. They’re using collaborative robotics applications and robotic process automation to get better at work.
Automation through robotic manufacturing processes and industrial robot simulation makes things faster and more reliable. It also cuts down on mistakes and makes supply chains better.
Adding machine vision integration and robot programming and control to cloud systems helps a lot. It makes remote monitoring and predictive maintenance possible. This makes industrial robotic systems more efficient and reliable.
This cloud-based approach to industrial robotics is a big chance for manufacturers. It helps them improve their operations and stay ahead in the fast-changing automation world.
The Transformative Power of Remote Robot Control
Remote robot control technology is changing the game in industrial robotics. It lets automation experts help more customers without being there in person. This boosts their productivity a lot.
With remote access, engineers can fix problems from anywhere. They can diagnose and solve issues without leaving their desk.
This new tech is a big deal for companies. It means they can trust their automation investments are being taken care of. Engineers can now quickly get production back on track. This makes them much more productive.
Multiplying Productivity with Remote Access
Remote robot control saves companies a lot of time. Industrial robots can be controlled from anywhere. This lets experts fix problems and improve performance without being there.
This new way of working could change how we use industrial robotics applications. It could make robotic systems much more productive.
Benefit | Impact |
---|---|
Remote robot control | Enables automation experts to serve more customers without physical presence |
Remote monitoring | Allows engineers to handle more troubleshooting calls and address issues faster |
Reduced downtime | Provides companies with the reassurance that their automation investments are being maintained effectively |
Increased productivity | Allows integrators to get production up and running again faster than ever before |
Digital Twins: Enabling Smart Manufacturing
In the era of Industry 4.0, digital twins have changed the game for manufacturers. They offer a virtual look at physical systems, using real-time data and advanced models. This gives a complete view of manufacturing assets and processes.
Digital twins help improve performance and cut downtime. They also boost efficiency and support better decision-making. They are key to smart manufacturing, helping optimize shop floor operations and more.
The need for better visibility and control in manufacturing has grown. Digital twins meet this need by combining cyber-physical systems and the industrial IoT. They help simulate, analyze, and optimize operations, boosting productivity and competitiveness.
Big names like Mars, General Electric, and Siemens are seeing the big picture. Mars has improved its supply chain with Microsoft’s Azure Digital Twins. General Electric uses digital twins for aircraft engine maintenance. Siemens has merged 3 factories into 1, saving space and reducing waste.
More companies are jumping on the digital twin bandwagon. About 75% of advanced industries are already using them. Digital twins are set to change the manufacturing game, making it smarter and more efficient.
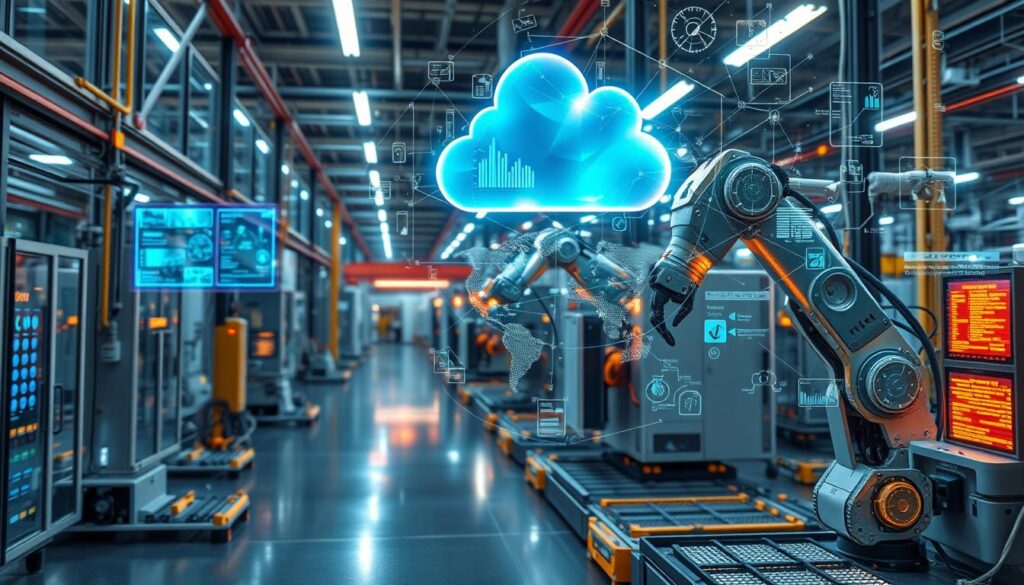
The Rise of Cloud-Based Digital Twins
The digital twin revolution is growing fast. It’s thanks to cloud computing, data analytics, and artificial intelligence (AI). Cloud-based digital twins (CBDTs) are becoming a key solution. They offer better remote accessibility, data processing and analysis, and scalability.
But, there are still challenges to overcome in CBDT research and use.
Overcoming Challenges with Cloud-Based Digital Twin Solutions
Current CBDT work often focuses on theoretical frameworks. It uses cloud infrastructure but overlooks practical details. The interaction between cloud and digital twin modeling is also not well-studied.
To tackle these issues, a new cloud-based digital twin framework is suggested. It combines cloud-enabled intelligence, digital twin modeling, and advanced visualization. This framework aims to bridge the gaps and offer a practical solution for digital transformation.
As the industry moves towards open-source software and cloud-based technologies, the future of digital twins looks bright. Overcoming current challenges will unlock CBDTs’ full potential. This will lead to higher productivity, efficiency, and innovation in many fields.
A General Cloud-Based Digital Twin Framework
The proposed general cloud-based digital twin (CBDT) framework aims to solve current CBDT research issues. It combines cloud-enabled intelligence like data processing, AI, and optimization with digital twin modeling and updates. It also includes visualization modules.
The modular design of the framework highlights the connections between these key parts. This design allows for remote accessibility, better data processing and analysis, and growth. It makes the framework scalable.
This CBDT framework uses cloud infrastructure to help create useful prototypes for industrial robotics. It avoids the need for expensive software platforms. This makes cloud-based digital twin simulation more accessible to small and medium-sized businesses.
- Cloud-enabled data processing and analysis capabilities
- Modular digital twin modeling and update modules
- Visualization and user interface for remote accessibility
- AI-powered optimization and decision-making algorithms
The CBDT framework connects these elements to offer a complete and scalable solution for industrial robotics. It helps businesses use the full potential of cloud-based digital twin technology.
Industrial Robotics Development: Upgrading Legacy Systems
Industrial robotics has changed manufacturing a lot. It has made things more efficient, accurate, and productive. Now, companies need to update their old systems with new robotics.
A new idea called the cloud-based digital twin (CBDT) helps with this. It makes old systems better by adding remote monitoring and control. This way, companies can use their robots better, work faster, and make fewer mistakes.
This article also talks about a real example of using CBDT. It shows how to make an old robot system better. This example teaches us how to use CBDT for more than just watching and controlling. It opens up new ways to improve robotics.
Key Metric | Improvement Achieved |
---|---|
Manual, time-consuming tasks | 74% decrease |
Workflow efficiency | 63% improvement |
Data accuracy | 92% increase |
Reduction in errors and anomalies | 85% decrease |
User interface and accessibility | 58% enhancement |
Compliance improvement | 79% increase |
Security measures for sensitive data | 81% increase |
Process speed | 70% increase |
Interoperability success rate | 89% increase |
Scalability and flexibility | 95% increase |
The case study shows how CBDT can change things. It helps companies use their old systems with new robotics. This way, they can do more with their robots, work smarter, and stay ahead in the smart manufacturing world.
Enabling Data-Driven Optimization and Innovation
The data from industrial robots is key to making them better. Robot connectivity is the base for getting this data. It lets manufacturers improve their robots’ functions.
By linking robots to the cloud, companies can create fleet monitoring dashboards. These dashboards help solve problems and train machine learning models. They also run simulations for testing new features without high costs.
Using robot data is vital for operational excellence and innovation in robotics. It boosts productivity, efficiency, and competitiveness.
Harnessing Robot Data for Operational Excellence
Machine learning makes robots better at seeing, understanding, and moving. AI controls their actions and decisions. Robots learn from their environment, doing tasks on their own and adapting to changes.
Key Data-Driven Optimization Strategies | Benefits |
---|---|
|
|
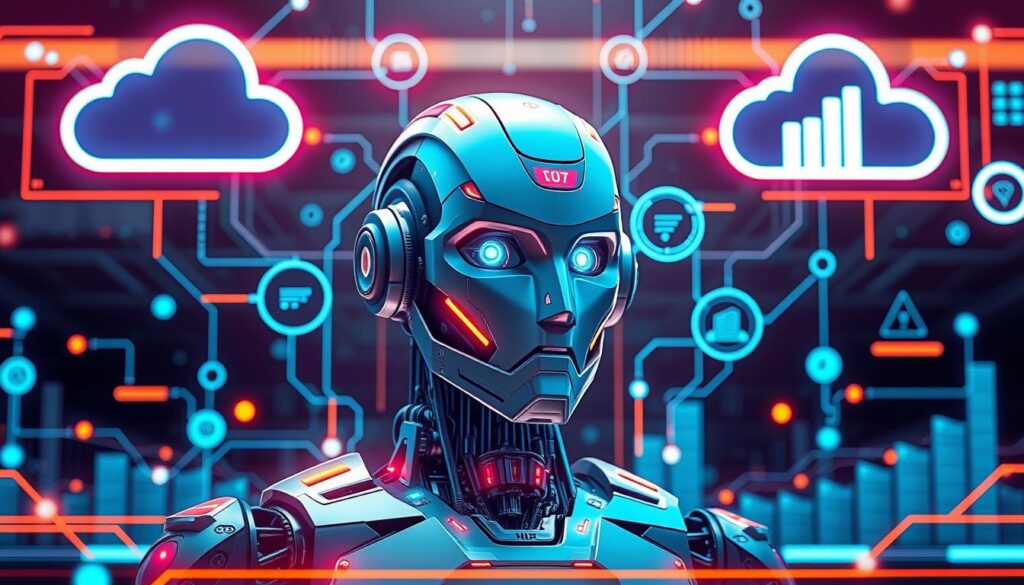
By using robot data, manufacturers can achieve operational excellence. This leads to more agility and innovation in automation. It helps companies make smart choices, improve processes, and stay competitive in the fast-changing robotics world.
Connecting ROS2 Robots to the Cloud
Connecting ROS2 robots to the cloud, especially with AWS IoT Core, helps manufacturers get valuable data. This data can improve their robotic systems. It also opens up new ways to use robots, like remote monitoring and data analysis.
To link ROS2 robots to the cloud, you need to set up secure authentication. You must download certificates and set up environment variables. Then, you can send data from the robot to AWS IoT Core using MQTT.
This connection between ROS2 robots and cloud platforms like AWS IoT Core is very powerful. It lets manufacturers use real-time data to make their robots better. They can find ways to improve and make decisions based on data.
Also, the cloud lets manufacturers watch and control their robots from anywhere. This means they can keep their robots running smoothly, fix problems quickly, and keep their systems reliable.
Keeping data safe is key when connecting to the cloud. Using X.509 certificates and AWS IoT Core’s security, manufacturers can protect their data. This keeps their operations safe from cyber threats.
In short, linking ROS2 robots to the cloud, especially with AWS IoT Core, is very beneficial. It offers remote monitoring, data analysis, and better security. This helps manufacturers get the most out of their robots and keep improving their work.
Conclusion
Integrating industrial robots with cloud-based systems for remote monitoring is a big step forward. It lets manufacturers use the cloud’s power to control robots from afar. This boosts productivity, makes troubleshooting easier, and improves control over robots.
Digital twins, especially cloud-based ones, are key to smart manufacturing. They give a complete view of assets and help make decisions based on data. A new framework for cloud-based digital twins can update old manufacturing systems and drive innovation in robotics.
Using robot data and connecting ROS2 robots to the cloud helps companies reach new heights. As the industrial robots market expands, combining cloud systems, digital twins, and data-driven optimization is crucial. It will shape the future of manufacturing and unlock the full potential of robotics.