In the fast-changing world of industrial robotics, engineers use hydraulic systems for heavy tasks. These systems provide the power and precision needed for big jobs in manufacturing, construction, and demolition. They are perfect for tasks that need a lot of force and power.
Engineers use advanced sensors and smart control algorithms to manage these complex systems. This lets them control the robots’ movements well. The robots can then work accurately, quickly, and efficiently.
Hydraulic systems are also very durable and strong. They work well in tough industrial settings. By using hydraulic systems, engineers are creating the next big robots. These robots are key to the Industry 4.0 revolution, bringing new tech to manufacturing and more.
Understanding Hydraulic Actuators
Hydraulic actuators are key in powering many industrial tasks, like heavy-duty robotics. They turn the energy in pressurized hydraulic fluid into motion. This lets machines move powerfully and precisely. The main idea behind hydraulic actuators is Pascal’s law. It says pressure in a closed, incompressible fluid is the same everywhere.
Principles of Hydraulic Actuation
Hydraulic systems have a pump, valves, a reservoir, and a cylinder or motor. The fluid, often a special hydraulic fluid, is pumped and controlled by valves. This moves a piston in the cylinder, creating motion. This motion powers many industrial uses, from building equipment to space parts.
Components of Hydraulic Systems
- Hydraulic pump: Creates the pressure needed to move the fluid.
- Hydraulic valves: Control the fluid’s direction, flow, and pressure. This lets the actuator move precisely.
- Hydraulic cylinder: Turns the fluid’s pressure into force and motion.
- Hydraulic fluid: A special fluid that carries power and lubricates the system.
- Hydraulic reservoir: Holds the fluid and helps cool and filter the system.
These parts work together well. They give hydraulic actuators their strong and reliable performance. This is important in heavy-duty industrial tasks, like robotics.
Advantages of Hydraulic Actuation in Robotics
Hydraulic actuators have many benefits for industrial robots. They can handle heavy tasks because of their high force and power density. This makes them perfect for tough industrial jobs.
High Force and Power Density
Hydraulic actuators are great at producing a lot of force and power. They can move more weight than electric or pneumatic systems. This means hydraulic robots can lift and move heavy loads easily, ideal for heavy-duty tasks.
Durability and Robustness
Hydraulic systems are known for being tough and reliable. They work well in harsh conditions and can handle heavy loads without breaking down. This makes hydraulic robots a solid choice for important tasks in manufacturing and construction.
Actuator Type | Force and Power Density | Durability and Robustness |
---|---|---|
Hydraulic | High | Robust |
Electric | Medium | Moderate |
Pneumatic | Low | Reliable |
Challenges in Hydraulic Systems Integration
Hydraulic actuation in industrial robots has many benefits. But, integrating these systems is not easy. The parts, like pumps and valves, add to the design and upkeep needs. Engineers must ensure these components work well together for the robot to perform efficiently.
Complexity and Maintenance Requirements
Hydraulic systems are more complex than others. This makes setting them up and keeping them running harder. Regular checks and fluid changes are key to keeping the system working right.
If these tasks are ignored, the robot’s reliability can drop. This can cause big problems in places where robots need to keep working without pause.
- 45% of survey respondents identified uncertainty about what technologies to use as the biggest challenge in implementing automation solutions.
- 25% of respondents mentioned that there is not enough industry information available to support automation implementation efforts.
- 88% of survey participants believe that opportunities exist for the fluid power industry as automation systems become more widespread.
When adding hydraulic parts to robots, engineers face another challenge. They must make sure the robot’s size and strength match the hydraulic system’s needs. Finding the right balance is hard, especially when space is tight.
The need for advanced hydraulic solutions in robotics is growing. To meet this need, we must tackle the system’s complexity and upkeep. This will help unlock the full power of hydraulic systems in heavy-duty robots.
Industrial robotics development
The world of industrial robotics has seen huge changes. It started with the Unimate robotic arm in the late 1950s. Since then, we’ve seen better sensors and the rise of collaborative robots (Cobots) in the 1990s and 2000s.
Today, we have more advanced robots thanks to better control systems and materials. As we want smarter manufacturing, robots will keep getting better. They will use new tech like machine learning and AI.
This change will make factories work better and faster. It will change how we use automation. We’re moving towards a future where humans and robots work together, known as “Industry 5.0.”
Milestone | Year | Significance |
---|---|---|
Unimate, the first industrial robot | Late 1950s | Marked the birth of the industrial robotics industry |
Mass production of the Unimate robotic arm | Early 1960s | Paved the way for widespread adoption in manufacturing |
Introduction of the Delta robot | 1980s | Significant leap in speed and precision for tasks like picking and packing |
Advanced sensors in robotic arms | 1990s and 2000s | Improved accuracy and flexibility in manufacturing operations |
Emergence of collaborative robots (Cobots) | 1990s and 2000s | Groundbreaking shift in the robotics industry, combining safety and efficiency |
Autonomous mobile robots | Recent years | Brought flexibility to material handling in industrial settings |
The future of industrial robotics is exciting. AI and IoT will be key in making things better. They will help robots learn and work better together. This will change how we make things and how we use robots in factories.
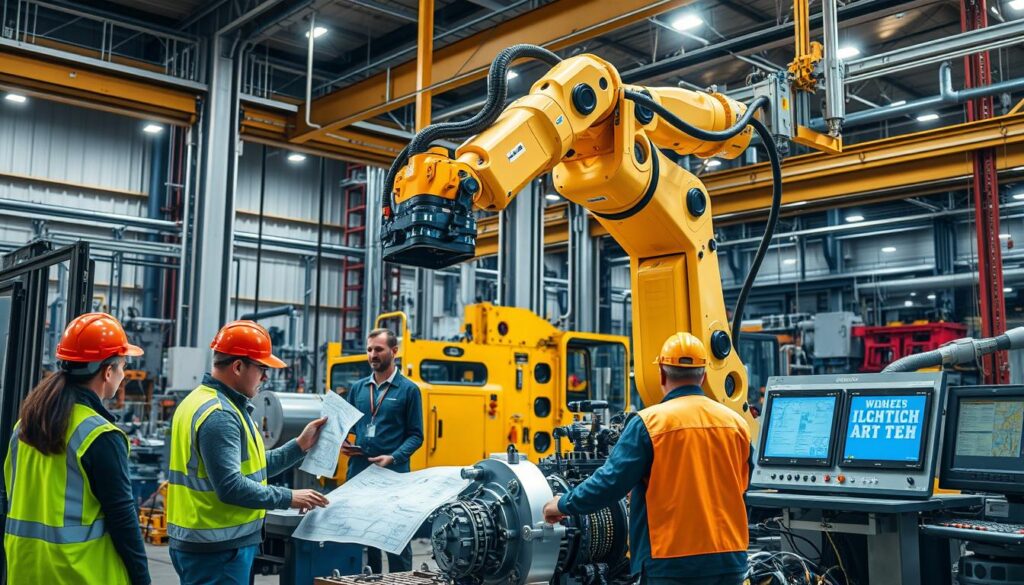
Applications of Hydraulic Robotics
Hydraulic robots are key in many industries, like heavy-duty manufacturing, construction, and demolition. They use hydraulic actuators for strength and durability. This makes them perfect for tough tasks.
Heavy-Duty Manufacturing
In manufacturing, hydraulic robots power big machines like presses and compactors. Their strength is unmatched, making automation easier. This was hard or impossible before.
Construction and Demolition
Hydraulic robots are also vital in construction and demolition. They handle heavy loads and work in tough places. This makes them reliable and boosts efficiency and productivity.
Application | Hydraulic Robotics Advantages |
---|---|
Heavy-Duty Manufacturing | High force and power density for driving large-scale equipment, such as presses, compactors, and material handling systems |
Construction and Demolition | Ability to handle heavy loads and operate in harsh environments, enabling tasks like lifting, pushing, and breaking down materials |
Hydraulic robots are essential in industry. They improve manufacturing, construction, and demolition. Their versatility and performance drive progress.
Advancements in Miniature Hydraulics
The world of industrial robotics has seen a big change with miniature hydraulic systems. These small and light solutions have made robots more versatile and easy to move. This has led to more efficient and agile industrial robots. Engineers have used compact hydraulic robots and lightweight hydraulic actuators to break size and weight barriers. Now, advanced industrial hydraulics can be used in many more places.
The hydraulic system miniaturization has been a big leap forward. It has made it possible to create robots that are both precise and strong. These miniature hydraulic systems have great power density and quick response. They are perfect for tasks that need detailed movements and a lot of force.
- Compact and lightweight hydraulic actuators have enabled the creation of more maneuverable industrial robots, expanding their potential applications.
- Advancements in materials and design have led to the development of highly efficient and durable miniature hydraulic components, reducing maintenance requirements and improving overall system reliability.
- The integration of hydraulic system miniaturization has been a key driver in the widespread adoption of advanced industrial hydraulics across various industries, from manufacturing and construction to human-assistive devices like exoskeletons.
As the industry keeps improving robotic abilities, miniature hydraulic systems will be key. They will help shape the future of industrial automation and more.
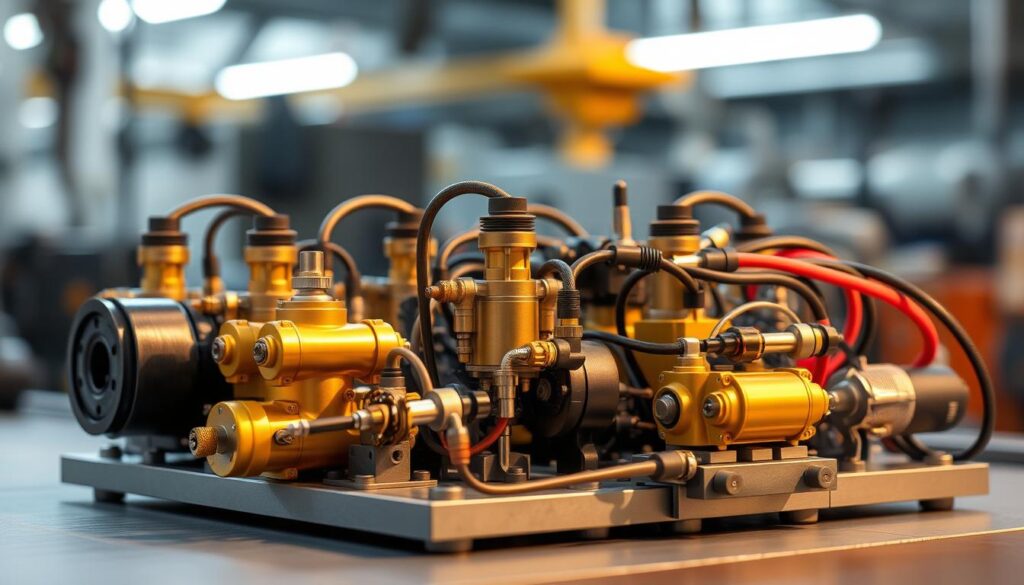
Conclusion
Hydraulic systems are key in using and controlling heavy-duty industrial robots. They give the power, force, and toughness needed for tough tasks in many industries. Adding hydraulic parts can be hard because of their complexity and upkeep needs. Yet, their high force and power, along with their strength, make them a top pick for many robotics jobs.
As robotics in industry keeps getting better, hydraulic systems will become even more important. New smart tech and better mini hydraulics will make these robots more flexible and powerful. This means they can do more tasks in the future.
Looking at hydraulic robotics and what’s coming in the future shows how vital these systems are. They help drive the growth and change in industrial automation. By using hydraulic systems, companies can stay ahead, work better, and meet the needs of today’s industry.