Designing industrial robots is a complex task. It involves quick progress in hardware, software, and automation. These robots have many parts, like control panels and sensors, all working together.
It’s important to think about what tasks the robot will do and where it will work. This helps in making the robot better for its job.
When making industrial robotics, we face issues like electromagnetic problems. This comes from the robot’s power needs and fast digital parts. Choosing the right connectors and cables helps solve these problems.
The robot’s robotic automation must be well thought out. This includes how much it can carry and move. It also needs to connect data and power smoothly.
Industrial robots work in tough places. They might face power spikes, extreme temperatures, or even shock. They need strong housing and connectors to keep out moisture and dust.
Adding sensors and machine vision is key. But, they must work well in harsh conditions. Communication is often wireless, using protocols like Ethernet or serial.
Power is another big thing in motion control and robot programming. We use special ways to manage heat and keep the robot quiet.
Introduction to Industrial Robot Design
Industrial robots are advanced computer systems that handle complex tasks. They are built with strong parts to work well in tough environments. The growth of industrial robotics is leading to big improvements in many areas. This is changing how factories and warehouses work.
Importance of Robotic Innovation
In 2020, the market for professional service robots grew by 12%. It reached $6.7 billion, as reported by the World Robotics 2021 report. The COVID-19 pandemic has made service robots more needed. They are now used for cleaning, food transport, and more.
This shows how robotic automation is useful in many fields. It’s not just for making things anymore. It’s also used in healthcare, security, and more.
Major Systems and Components
An industrial robot has many parts. These include a control panel, sensors, and a power system. All these parts must work well together.
The rise of collaborative robots (cobots) has made robots more useful. They can now work with people in smaller spaces. This is thanks to their ability to work safely without big fences.
There are six main types of industrial robots. These include robots that move in different ways. This variety helps manufacturers automate many tasks.
Key Robotic Innovation Trends | Adoption Drivers |
---|---|
Autonomous Mobile Robots (AMRs) for industrial use | Increased efficiency, reduced costs, and customized production lines |
Integration of robots into diverse sectors beyond manufacturing | Expanded applications in logistics, security, rescue, agriculture, and healthcare |
Development of collaborative robots (cobots) for human-robot interaction | Reduced safety requirements and enhanced flexibility in workspace utilization |
Remote control and skill-based robot training systems | Improved productivity, multi-control, and efficient factory operation |
Tasks and Operating Environment
When making industrial robots, we must think about the tasks they will do. We pick the right parts and set them up based on what they need to carry, move, and how they move. It’s also key to think about where the robot will work. Robots face things like power spikes, very hot or cold temperatures, and harsh chemicals.
The parts inside the robot, like the circuit boards and wires, need to be strong. They must handle these tough conditions so the robot can work well without stopping.
Identifying Automation Tasks
Industrial robots do many things, like welding, assembling, and moving things around. Choosing the right robot for a job means looking at what it needs to carry, move, and how precise it needs to be. FCC has used robots for over 80 years to make clutches better and faster.
Environmental Factors and Challenges
The place where a robot works is very important. Robots face issues like power spikes, extreme temperatures, and harsh chemicals. They also deal with shakes and bumps.
Designing strong parts for the robot is key. This way, the robot can handle these challenges and keep working without stopping.
Environmental Factor | Potential Impact | Design Considerations |
---|---|---|
Power Surges | Damage to electrical components | Surge protection, robust power supply |
Extreme Temperatures | Thermal stress, component failure | Thermal management, insulation, cooling systems |
Corrosive Substances | Corrosion of materials, component failure | Corrosion-resistant materials, protective coatings |
Mechanical Vibrations or Shocks | Structural fatigue, component damage | Shock-absorbing mounts, vibration-damping materials |
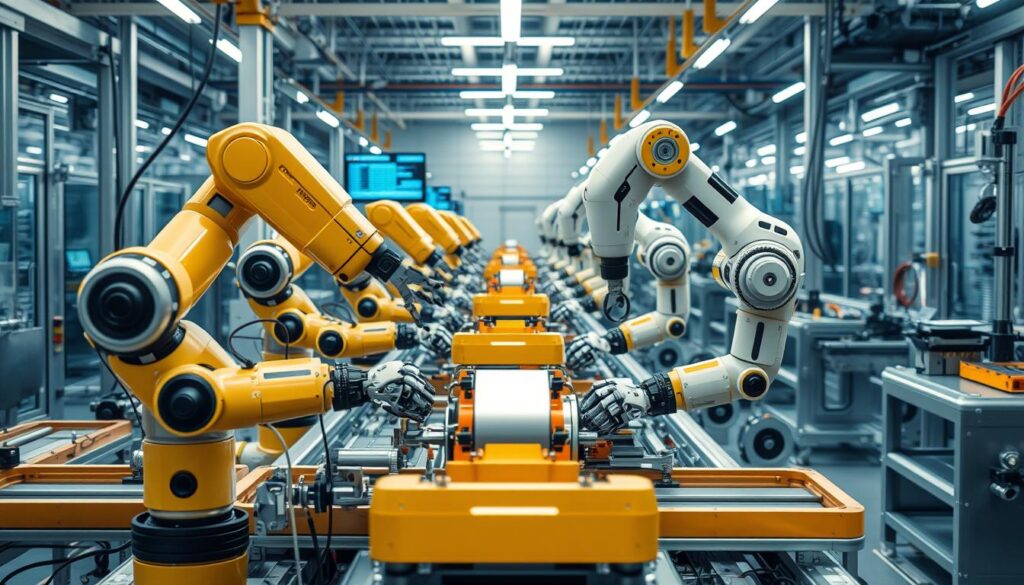
Sensors, Communications, and Networking
Advanced sensors and strong communication systems are key in modern industrial robotics. They help robots work well with other machines, people, and the environment. This leads to new ideas and better work in many fields.
Sensor Integration and Vision Systems
Sensors are crucial for industrial robots, both inside and outside. They take measurements and help robots interact. It’s important to pick sensors that can handle tough conditions well.
Machine vision systems use cameras and smart algorithms. They help robots see and do things like recognize objects, measure sizes, and check quality.
Communication and Networking Protocols
In industrial settings, many protocols are used for communication, like wireless, CANBus, Ethernet, and serial. It’s vital to have fast and reliable data transfer, especially for quick and frequent tasks. Strong connectors and cables are needed to keep these connections safe.
Communication Protocol | Advantages | Applications |
---|---|---|
Wireless (Wi-Fi, Bluetooth, 5G) | Flexibility, mobility, reduced cabling | Remote control, data transmission, cloud computing |
CANBus | Real-time, deterministic, reliable | Motion control, sensor integration |
Ethernet | High-speed, scalable, widespread adoption | Robot programming, robotic system integration |
Power Delivery and Thermal Management
Creating industrial robotics needs careful focus on power delivery and thermal management. As robots get smaller and more compact, engineers face new challenges. They must ensure efficient power delivery and manage the heat these machines produce.
Power delivery is vital in robotics. The system’s power management and its parts need a steady power supply. New power system designs aim to meet these needs without causing noise or heat.
Thermal management is also crucial. The system’s components, like motors and electronics, must not overheat. Using heat sinks and special materials helps keep the system cool. This also reduces electromagnetic interference.
Overcoming power and thermal challenges is key to making industrial robots work well. By using new power and cooling solutions, designers can make robots that meet today’s industry needs. These advancements will help shape the future of industrial robotics development.
Industrial robotics development
The journey of industrial robotics has seen big changes in technology and design. It started with the Unimate in the late 1950s. Now, we have advanced cyber-physical systems and the Internet of Things. This shows how much the industry has grown.
Robotic Arm Design Considerations
Designing robotic arms is key in industrial robotics. We must think about payload capacity, motion range, and the type of motion. This ensures the arm works well for tasks like welding and assembly.
Collaborative Robot (Cobot) Integration
Collaborative robots, or cobots, are made for working with humans. They have safety features like force limiters. This lets them work safely with people, making cobots a big deal in industrial robotics.
The use of cobots in factories is a big step. It boosts productivity and keeps workers safe. The world of industrial robotics keeps getting better, thanks to robotic automation, collaborative robots, and robotic system integration. As we move into Industry 4.0, robots will play a bigger role in making things.
Safety Risks and Mitigation Strategies
The industrial robotics industry is booming, with a record 553,052 installations worldwide in 2022. Ensuring the safety of these advanced systems is crucial. Industrial robots, powered by high-voltage electrical systems, pose safety risks like unexpected movements and system failures.
Common Safety Hazards
The rise of industrial robots, collaborative robots, and advanced robotics systems in various settings has made safety measures essential. Common safety hazards include unexpected robot movements, system failures, and electrical hazards.
- Unexpected robot movements can cause collisions with workers or other equipment.
- System failures can lead to uncontrolled robot behavior.
- Collision hazards between robots and humans or other objects are a concern.
- Electrical hazards, such as electric shock or fire, are risks due to high-voltage systems.
Implementing Preventive Measures
To address these safety risks, a comprehensive approach is needed. Strategies include:
- Thorough risk assessment to identify hazards and develop safety protocols.
- Installing safety guards, emergency stop buttons, and barriers to restrict access.
- Using safety sensors and machine vision systems to detect and respond to hazards.
- Providing employee training and fostering a strong safety culture.
- Following industry standards, like ANSI/RIA R15.06-2012 and ISO 10218-1 and ISO 10218-2, for safe robot systems.
By taking these steps, industries can safely use industrial robots and collaborative robots. This ensures the well-being of workers and a safe work environment.
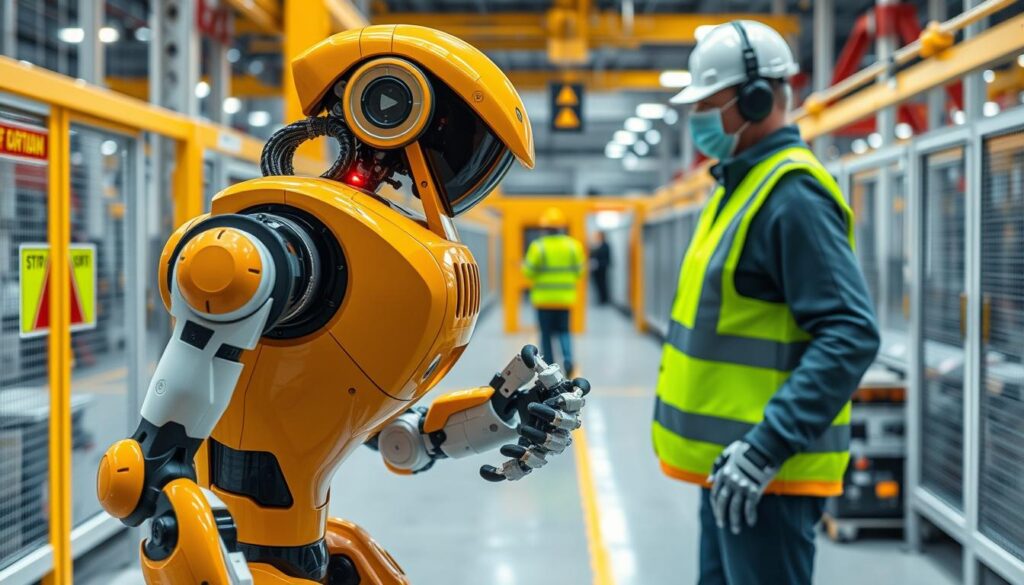
Regulatory Compliance and Industry Standards
Keeping industrial robots safe is a big challenge. It’s not just about the latest safety tech. Following rules and standards is key to protecting workers and using industrial robot safety systems right.
OSHA and General Industry Standards
OSHA doesn’t have specific rules for robots yet. But, it does follow general rules for all workplaces. These rules require safety measures, training, and upkeep to lower risks.
ANSI/RIA and ISO Robot Safety Standards
The American National Standards Institute (ANSI) and the Robotic Industries Association (RIA) have made their own robot safety rules. They also follow ISO standards like ISO 10218-1 and ISO 10218-2. These standards cover many industrial robot safety areas.
These standards help make sure robots are safe for people. They also keep up with new tech like cobots and mobile robots.
Standard | Overview |
---|---|
ANSI/RIA R15.06-2012 | Provides comprehensive guidelines for the safe design, implementation, and operation of industrial robot systems. |
ISO 10218-1 and ISO 10218-2 | Establishes safety requirements for the design and integration of industrial robots, covering both robot manufacturers and system integrators. |
ISO 9001 and ISO 14001 | Enhance quality, safety, and environmental management in industrial robotics to ensure effective processes and high-quality, sustainable products. |
Following these rules and standards shows a company cares about industrial robot safety. It builds trust in the robotics field. And it makes sure these advanced tools are used safely at work.
Conclusion
Creating industrial robots is a complex task. It involves mechanical, electrical, and software systems. Each part needs special attention. As more businesses want automation, following standards and safety rules is key. This will help humans and robots work well together.
The robot industry is set to hit $3.7 billion by 2021. This growth comes from more companies using robots to save money. Robots have made production faster, cheaper, and created new jobs in programming and engineering.
Software like machine learning and AI is making robots smarter. They can learn and make choices on their own. With more robots in factories, productivity is going up. This means a bright future for robots in making things better and growing the economy.