In today’s fast-changing world, industrial robotics is key to making processes better and more efficient. Robots help in many fields, from making things to farming, by automating tasks and boosting productivity. But, making these robots last in tough conditions is a big challenge for engineers.
Extreme temperatures, high humidity, dust, and vibrations can harm robots. Engineers use a mix of cooling systems, thermal management, and smart programming to keep robots running without overheating. This approach makes robots work better and safer in tough environments.
Engineers use new tech in machine learning, AI, and design to solve these problems. They create strong cooling systems and manage heat well. They also set up systems to watch and control robots, so they can keep working without overheating.
Thanks to these efforts, robotics is getting better and better. Robots are becoming more reliable and efficient, even in the toughest places. As robotics gets smarter, the future of work looks bright, with more productivity, safety, and green practices in many industries.
Understanding Environmental Challenges in Industrial Robotics
As industrial robotics grow, engineers face many environmental challenges. These include extreme temperatures, high humidity, dust, and vibrations. Knowing these challenges helps make robots more durable and efficient.
Extreme Temperatures
Extreme temperatures can harm industrial robots’ electronics and motors. Heat can cause them to overheat and wear out faster. Cold can make them move less and malfunction. Keeping robots cool or warm is key to their performance.
High Humidity
High humidity can damage industrial robots, causing corrosion and electrical failures. They need strong seals and enclosures to protect against moisture. This ensures they work well in damp or humid places.
Dust and Debris
Industrial areas often have dust and debris that can harm robots. This can clog sensors and make parts move poorly. Good filters and seals are needed to keep robots clean and working well.
Vibrations
Vibrations and shocks in industrial settings can wear down robots. Strong designs and shock-absorbing parts help them last longer. This keeps robots running well, even in tough environments.
By tackling these challenges, engineers can make robots that work well in harsh conditions. They use new designs, materials, and monitoring to improve robots. This helps the robotics industry grow while being kind to the environment.
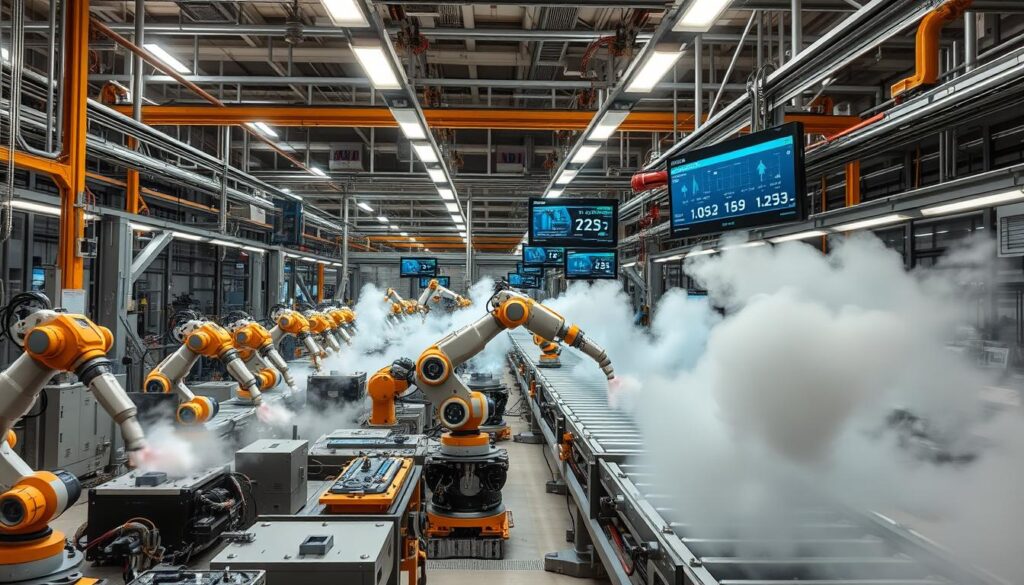
Design Strategies for Durable Industrial Robots
The need for industrial robots is growing fast, with over 373,000 sold in 2019. Making them last in tough places is key. Using strong materials, sealing well, and managing heat are important steps. These help robots handle hard work without breaking down.
Selecting Robust Materials and Components
Choosing the right materials and parts is crucial for durable robots. They need to handle temperature changes, moisture, and corrosion well. Also, picking high-quality parts for the robot’s job is key for steady work.
Implementing Effective Sealing and Enclosures
Keeping robots safe from dust, water, and other dangers is essential. Rubber gaskets, O-rings, and seals help block these threats. They protect the robot’s inside parts and electronics from harm.
Enhancing Thermal Management
Keeping robots at the right temperature is important, especially in harsh places. Solutions like heat sinks, fans, and insulation help control temperature. This stops overheating and keeps the robot working well.
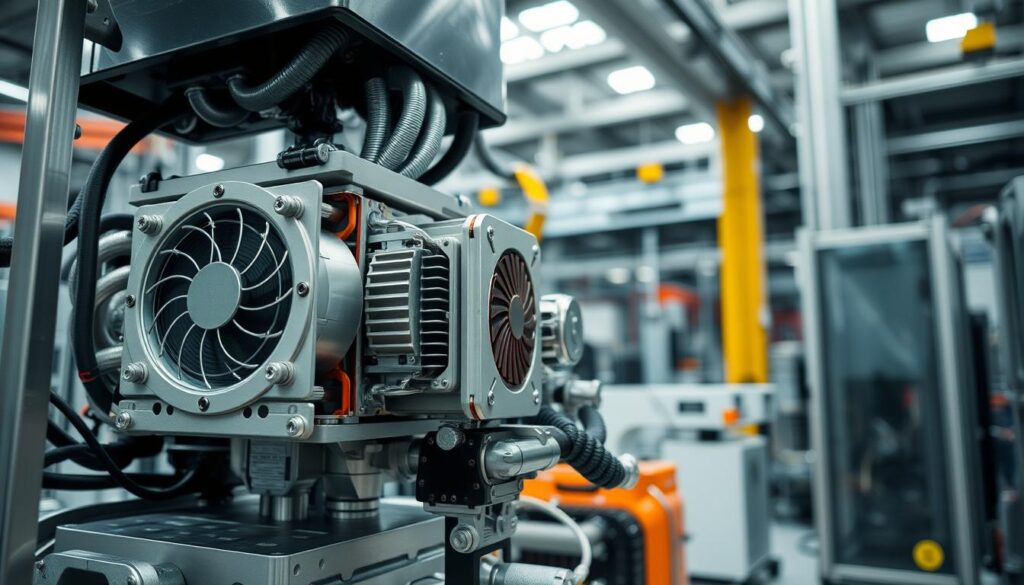
By using these design strategies, makers can build robots that last. These robots can handle tough jobs and keep working well for a long time.
Industrial robotics development: Integrating Environmental Sensors and Monitoring Systems
As the field of industrial robotics grows, engineers focus more on adding environmental sensors and monitoring systems. These tools help robots work well in tough environments. They make sure robots can keep running smoothly.
The latest IFR World Robotics 2023 report shows electronics, automotive, and pharmaceuticals lead in using robots. But, robots are now also in retail, e-commerce, aerospace, and recycling. This shows robots are becoming more versatile.
Adding sensors and monitoring systems is key for robots to handle harsh conditions. These tools track things like temperature, humidity, and dust. This lets the robot adjust to keep working well.
Combining automation and robotics is vital for green manufacturing. It’s a big change in how things are made. Using green energy, tracking products better, and flexible production are all part of this shift.
Autonomous mobile robots, with Industry 4.0 tech, boost productivity and help the environment. Sensors and monitoring systems are essential for this. They help robots work well in many places.
Sensor Type | Cost Range | Maintenance Considerations |
---|---|---|
Basic Proximity Sensors | $10 or less | Regular calibration and checking |
Advanced Vision Systems or LIDAR | Tens of thousands of dollars | Potential for data interpretation errors |
As robotics gets better, adding sensors and monitoring systems is crucial. It helps robots last longer, work better, and be more eco-friendly. Robots can then help make things in a greener way.
Adopting Robust Mechanical Designs
In the world of industrial robotics, keeping robots running without overheating is key. It’s not just about picking strong materials. It’s also about making the robots’ designs tough for harsh environments. This way, engineers can build robots that last through tough conditions.
Reinforcing Structural Components
The strength of a robot starts with its structure. Making sure key parts can handle stress and impacts is vital. This might mean using stronger materials, adding bracing, or changing the design. By doing this, engineers can make robots last longer and work better.
Shock Absorption and Vibration Damping
Robots in industrial settings face shocks and vibrations that can wear them down. Adding features to absorb these shocks and vibrations helps a lot. This could be through dampeners, isolators, or flexible parts that soak up the energy.
By focusing on strong designs, reinforcing parts, and adding shock and vibration control, engineers make robots that can handle tough jobs. This makes the robots more reliable and longer-lasting in the field.
Conclusion
Making industrial robots last in tough environments is a big challenge. It needs a mix of strategies. Engineers must know the obstacles like extreme weather, high humidity, and dust.
They can then design better machines. Using strong materials and good seals helps a lot. Also, keeping the robot cool is key for its long life.
Adding sensors and monitoring systems helps a lot. They let robots work better and need less fixing. Strong designs and shock absorption also make robots more durable.
As robots get better, they’ll work in harsh places more easily. This opens up new chances in many fields. By making robots last longer, we can make factories work better and more efficiently.