Robotic actuators are the key “muscles” of industrial robots. They turn stored energy into motion. This is vital for many tasks, like robotic automation systems and machine vision integration. The right actuator can make a robot faster, more precise, and more efficient.
Electric actuators are often used because they are fast, precise, and easy to control. DC motors, like stepper motors and servo motors, are reliable and common. Brushless DC motors are also popular for their efficiency and long life.
Hydraulic actuators are great for heavy tasks because they have a lot of power. They work by using pressure in a fluid to move. Pneumatic actuators use air to move and are simple, light, and affordable.
Choosing the right actuator is key for industrial robots. It affects how well the robot works in tasks like industrial internet of things (IIoT) and human-robot collaboration (HRC). Knowing what each actuator can do helps engineers make robots better and meet industry needs.
The Vital Role of Actuators in Robotics
Robotic actuators are like the “muscles” of robots. They let robots move and do many tasks. These parts connect a robot’s control systems to the real world, turning digital signals into real movements.
Actuators are key in many areas, like industrial automation and medical robotics. They make robots versatile and powerful.
Actuators: The Dynamic “Muscles” of Robots
There are many types of robotic actuators, each for different uses. Linear actuators are super precise, great for tasks needing high accuracy. Soft actuators are flexible and work well for delicate tasks, like surgeries and farming.
Enabling Robots to Interact with Their Environment
Actuators do more than just move robots. They work with sensors and control systems for better performance. This lets robots move and act on their own in changing situations.
Robotic actuators are crucial for robots to interact with their surroundings. For example, a robotic arm in a factory needs to move accurately to handle items. This is thanks to high-quality actuators.
In short, actuators make robots come to life. They connect the signals a robot gets to its actions. Knowing about actuators is key to understanding robotics.
Industrial robotics development: Actuator Types and Operating Principles
In industrial robotics development, actuators are key. They help robots move and work with their environment. This is thanks to machine vision integration and collaborative robot programming.
Actuators make robots move by following signals from the control system. They can do simple tasks or complex ones, like moving a robotic arm in intelligent manufacturing processes.
There are many types of actuators used in robots. Electric motors are popular for their efficiency and precision. Hydraulic pistons are strong and good for heavy tasks. Pneumatic cylinders are simple and fast, perfect for quick, repetitive tasks in industrial automation.
New tech in sensor fusion techniques and robotic control architectures has improved robots. They can now work better with industrial internet of things (IIoT) and human-robot collaboration (HRC). This makes them more efficient and accurate in many manufacturing tasks. It also helps in predictive maintenance strategies to keep robots running well for longer.
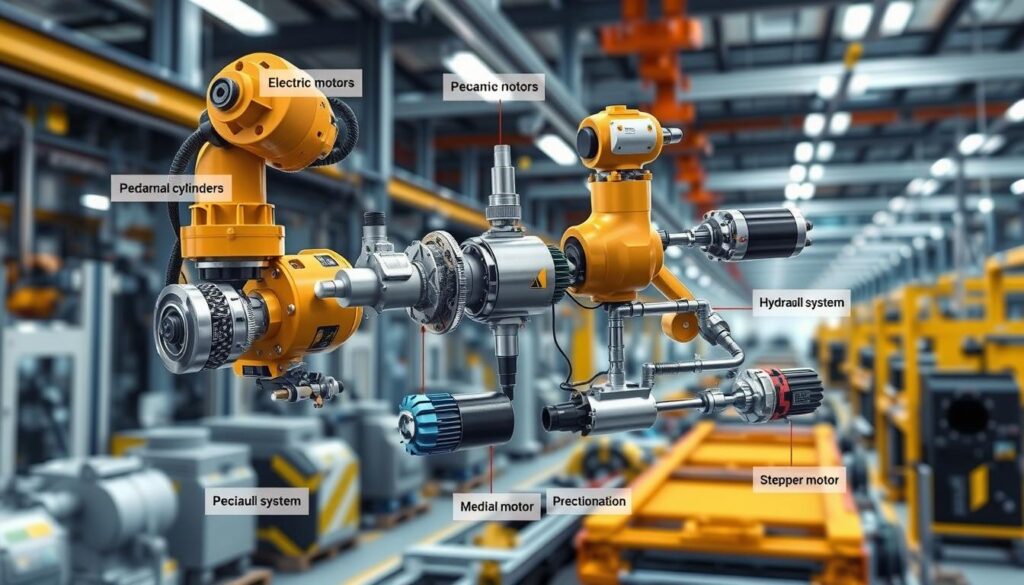
Choosing the right actuators depends on the task’s needs. It looks at the application, payload, speed, and precision. As industrial robotics development grows, so will actuator tech. This will shape the future of robotic automation systems and their role in intelligent manufacturing processes.
Electric Actuators: Precision and Speed
Electric actuators are key in robotic automation, known for their precision and speed. They use electric motors to move, driving many advanced robots and systems. These tools are changing how we make things and automate tasks.
Working Principles of Electric Actuators
An electric actuator works by using an electric motor. This motor creates rotary motion. Then, it turns into linear or other motions through gears, belts, or screws.
This setup lets electric actuators move quickly and accurately. They’re perfect for tasks like moving a robotic arm or controlling a surgical robot.
Advantages and Applications of Electric Actuators
- High speed and precision: Electric actuators move fast and accurately. They’re great for tasks needing tight control and quick responses.
- Ease of control: Electric motors and advanced systems make controlling them easy. This makes them fit well in robots and control systems.
- Versatility: They can handle many types of motion, from assembly lines to surgical robots.
Because of these benefits, electric actuators are everywhere in robotic automation, industrial automation, and more. They power fast and precise movements in CNC machining and the gentle actions of soft robotics in healthcare.
Hydraulic Actuators: Power and Durability
In the world of industrial robotics, hydraulic actuators stand out. They are known for their strong force and torque. This makes them perfect for robotic automation in construction robotics, demolition robotics, and more. Hydraulic actuators can handle tough tasks in rugged environments for industrial robots.
Hydraulic actuators work by Pascal’s law. This law says pressure in a fluid is the same everywhere. A pump pushes oil to move a piston. This piston can then move things in a line or circle, useful for many industrial robots tasks.
Hydraulic actuators have many benefits. They are strong and last long, great for heavy tasks. They can also handle tough conditions and heavy loads. This makes them reliable for challenging environments.
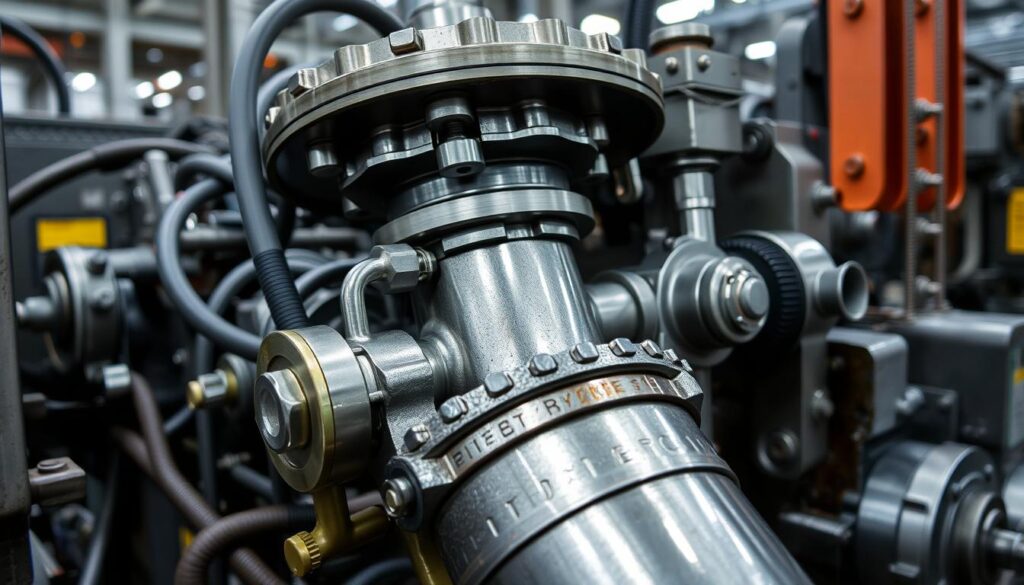
The need for advanced robots is growing. Hydraulic actuators will keep playing a key role. Their strength, durability, and flexibility are vital for new robotic solutions in many fields.
Pneumatic Actuators: Simplicity and Cost-Effectiveness
In the world of industrial robotics, pneumatic actuators are gaining popularity. They offer a mix of simplicity and cost-effectiveness. These actuators use compressed air to move, fitting well in many tasks like assembly and packaging.
The Advantages of Pneumatic Actuators
Pneumatic actuators work by expanding compressed air, which pushes a piston or diaphragm to move. Their simple design and use of air as a power source make them cost-effective. This makes them a good choice for robotic systems.
One big plus of pneumatic actuators is their lightweight build. This leads to lower costs and easier integration into robots. Their simple design also means less maintenance and more reliability. They’re great for tasks like material handling, packaging, and sorting.
These actuators are also good for tasks needing repetitive, high-speed movements. Their air-based operation allows for quick responses and precise control. This is perfect for tasks needing consistent performance and efficiency in industrial automation and robotic automation.
Advantage | Explanation |
---|---|
Simplicity | Pneumatic actuators have a straightforward design with fewer moving parts, making them easier to maintain and less prone to mechanical failure. |
Low Cost | Pneumatic actuators utilize readily available and cost-effective compressed air as their power source, resulting in a lower overall cost compared to other actuator types. |
Lightweight | The lightweight construction of pneumatic actuators makes them easy to integrate into a wide range of robotic systems, enhancing flexibility and mobility. |
Repetitive High-Speed Movements | Pneumatic actuators excel at performing repetitive, high-speed movements, enabling consistent performance and efficiency in industrial automation and robotic applications. |
As the need for industrial automation and robotic automation grows, pneumatic actuators stand out. Their simplicity, low cost, and lightweight design make them ideal for many tasks. This includes material handling, packaging, and sorting.
Selecting the Right Actuator for Your Robot
Choosing the right actuator is key to a robot’s success. Actuators are like muscles that let robots move and do tasks. The right actuator depends on power source, motion type, and precision needed.
Factors to Consider When Choosing an Actuator
The power source is very important. If you have electricity, electric actuators are great for their precision and efficiency. But, if electricity is hard to find, hydraulic or pneumatic actuators work well with other power sources.
The motion type needed is also crucial. Linear actuators are best for straight movements, while rotary actuators are great for turning. Knowing your robot’s motion needs helps pick the right actuator.
Precision is another big factor. Electric actuators are more precise than hydraulic or pneumatic actuators. This makes them better for tasks needing exact control.
Think about safety and upkeep too. Hydraulic actuators might need more care than electric actuators.
Actuator Type | Power Source | Motion Type | Precision | Maintenance |
---|---|---|---|---|
Electric | Electricity | Linear, Rotary | High | Low |
Hydraulic | Fluid Power | Linear, Rotary | Medium | High |
Pneumatic | Compressed Air | Linear, Rotary | Medium | Medium |
By thinking about these points, you can find the best actuator for your robot. This ensures your robot works well, efficiently, and reliably.
Conclusion
The growth of robotic actuators has led to big changes in industrial robotics and automation. From the first Unimate robot to today’s advanced robots, different actuators have changed how we make things. They make work faster, safer, and more efficient.
Choosing the right actuator for each job is now key in robotics. Electric actuators are great for precise and fast work. Hydraulic actuators have lots of power and last a long time. Pneumatic actuators are simple and save money. By knowing what each actuator does best, makers can make better robots for today’s factories.
The future of robotics looks bright with new tech like AI and the Internet of Things. These advancements will make robots even more useful in factories. As we keep improving actuator technology, the manufacturing world will get even better. This will help factories work smarter and compete globally.