The use of industrial robotics development in manufacturing has changed the game. It brings more efficiency, precision, and productivity. But, there are big challenges on the way to success. These include the high cost of robotic automation systems, making them hard to fit into current workflows. Also, programming them is complex, and you need skilled people to do it.
There’s also the worry about keeping workers safe around these machines.
The cost of industrial robotics is a big problem. It’s expensive, especially for small businesses. They struggle to afford the robots. They have to keep making things and selling them to pay back the cost of the robots.
Adding machine vision technology and collaborative robot programming to production is tough. It’s hard to get everything to work together smoothly. The lack of standard robot controller software makes it even harder.
New tech raises safety concerns. There are strict rules and big fines for not following industrial robot safety standards.
Keeping workers safe when robots and humans work together is key. It’s also important to train employees to use industrial robot kinematics safely. This ensures a safe work environment.
Current robotics aren’t very flexible. They’re not made to be easily changed or reused. This makes it hard to adjust to new production needs. To overcome this, careful planning is needed. It’s important to make sure robots work well with people and fit into the workflow smoothly.
The Rise of AI in Manufacturing
Artificial intelligence (AI) is changing the manufacturing world. It’s improving quality control, product development, and supply chain management. AI, machine learning, and robotic process automation are making operations better and more efficient.
Enhancing Quality Control and Product Development
AI is making quality control better. It uses automated visual inspections and real-time defect detection. This helps manufacturers find and fix problems fast, reducing waste and improving product quality.
In product development, AI is a game-changer. It helps with prototyping, simulation, and optimization. This means manufacturers can innovate faster, design better, and get new products to market quicker.
Optimizing Supply Chain and Logistics
AI is also changing supply chain management and logistics. It uses predictive maintenance and autonomous intelligence. This leads to better inventory management, order fulfillment, and transportation planning.
Key Metric | Current Value | Projected Value (5 years) |
---|---|---|
Global Industrial Robots Market Size | $55 billion | $75 billion |
Industrial Robots in Operation Worldwide | 2.7 million | 3.5 million |
Robot Installations in China | 52% of global share | 55% of global share |
The growth of artificial intelligence, machine learning, and robotic process automation is transforming manufacturing. It’s leading to better quality control, product development, and supply chain management. As these technologies become more common, we’ll see even more efficiency, productivity, and competition in the manufacturing world.
Costs and Investment Hurdles
Implementing industrial robotics comes with a big price tag. Buying top-notch robotic systems and the needed software is expensive. This can stop smaller companies or those with small budgets from starting.
But, the benefits down the line are worth it. You can make more products and save on labor costs. This makes the initial cost worth it in the long run.
A study found that 33% of respondents said they couldn’t afford mobile robots. Setting up a whole warehouse with robots could cost around $1 million. Yet, the market for mobile robots is growing fast. It’s expected to hit $14 billion by 2027, showing there’s a big demand and potential for profit.
Metric | Value |
---|---|
Projected market revenue for mobile robots (2027) | $14 billion |
Projected mobile robot sales (2027) | 700,000 units |
Projected increase in mobile robot sales (2023) | 25% |
Companies with revenues over $1 billion using mobile robots | More likely than smaller companies |
Companies partially automating workflows with mobile robots | 71% |
The upfront costs for industrial robotics and AI hardware and software are high. This is especially true for SME manufacturing automation challenges. But, the long-term gains can make the investment worthwhile.
Options like financing, leasing, and pilot projects can help. They make it easier for smaller businesses to try out automation and see its benefits.
Data Management and Security Concerns
The fast growth of AI in manufacturing has led to more data from IoT sensors. This data is key for better productivity and quality. But, it also brings big challenges in managing and securing this data.
Navigating the Data Deluge
Managing industrial IoT data is getting harder. Manufacturers must store, organize, and analyze lots of data from robots. They need to break down data silos, ensure data quality, and follow strong data rules to use this data well.
Safeguarding against Cybersecurity Threats
Industrial robots are more connected now, making cybersecurity for industrial robots very important. To protect against threats, manufacturers need a solid security plan. This includes access controls, keeping software up to date, and secure networks.
Cybersecurity Challenges | Impact on Manufacturing |
---|---|
Poor Identity and Access Management (IAM) | Untrained operators making changes that introduce safety or manufacturing issues |
Vulnerable operating systems and software | Increased risk of firmware and software attacks, propagation of security flaws |
Insecure communication channels | Potential for data breaches and disruption of production processes |
To tackle these manufacturing data security issues, manufacturers should do regular security checks. They should also use strong access controls and watch out for new cyber threats.
Industrial robotics development
Advanced artificial intelligence (AI) in industrial robots brings new challenges. Skilled programmers are needed to handle the complex programming. Making sure new robots work with old machines is a big task that needs teamwork with robotics experts.
The Delta robot’s introduction in the 1980s was a big step forward. It made picking and packing faster and more precise. Later, better sensors in the 1990s and 2000s made robotic arms more accurate and flexible. Now, we have Collaborative Robots (Cobots) that work with humans, making work safer and more efficient.
Navigating the Complexities of Industrial Robot Programming
Adding AI to industrial robots is tough. Here are some main challenges:
- Skilled Programmers: Finding experts in robotic programming and AI is hard. The programming is complex.
- Compatibility with Existing Machinery: Making new robots work with old machines needs careful planning and teamwork.
- Adaptability and Flexibility: Current robots are not very flexible. They can’t easily change to meet new production needs.
The industrial robotics field is growing fast, thanks to AI and IoT. To make the most of industrial robot programming, robotic system integration, and AI-enabled industrial robots, companies need to overcome these challenges. With the help of robotics programming experts, they can boost productivity, automation, and save costs.
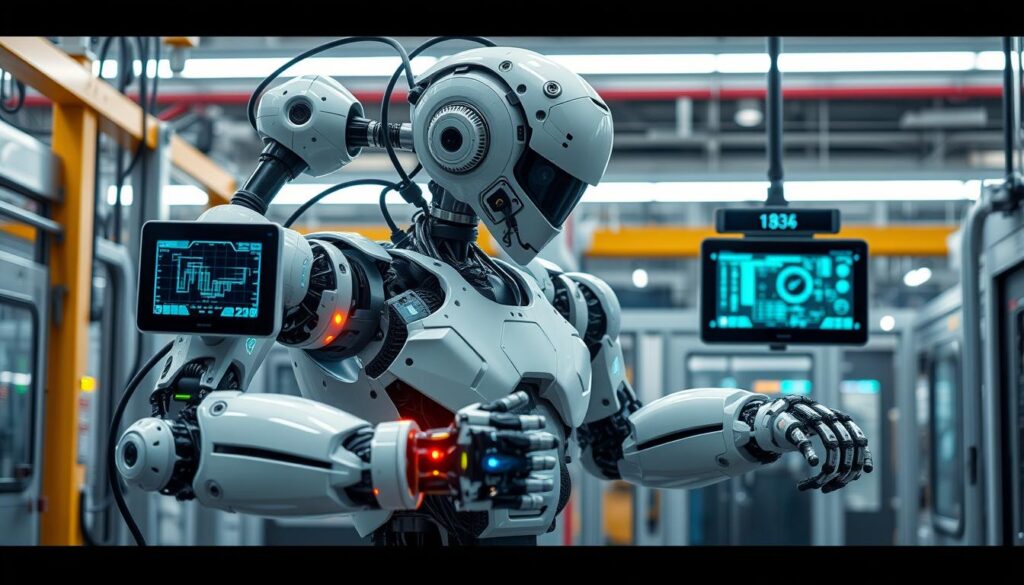
Safety and Workforce Considerations
As industrial robots become more common, keeping workers safe is a big challenge. It’s important to have strong safety measures and train workers well. This way, they can work safely with these machines.
Enhancing Industrial Robot Safety
Adding safety features like sensors, emergency stop systems, and safety barriers is key. These help prevent accidents and reduce risks. They make sure humans and robots can work together safely.
To keep everyone safe, we need to find and fix potential dangers. We also need to follow rules from groups like OSHA and ISO. This ensures robots are safe in the workplace.
Workforce Training and Upskilling
- It’s crucial to train workers well for automation. This helps them work safely with robots.
- Teaching safety, emergency response, and how to use robots is important. It keeps the work area safe.
- Upskilling for Industry 4.0 helps workers keep up with new tech. They learn skills needed for automated factories.
By focusing on safety and training, companies can make robots work well. This creates a safe and skilled team ready for new automation.
Flexibility and Adaptability Issues
The current state of robotics has big problems. It’s hard to change or reuse industrial robots because they’re not made to be flexible. This makes it tough to adjust manufacturing lines when production needs change.
Adaptive robotics technology helps robots learn and adjust on their own. This means they can work better in changing environments without needing humans to help. But, making robots smart enough to make decisions in real-time is still a big challenge.
Flexibility in robots means they can change how they work when things change around them. The right algorithms and design changes can make robots more adaptable. This lets them learn and do new tasks, even if they don’t know the details beforehand.
Using adaptive robotics can make production better, safer, and more efficient. It helps robots and humans work together better. This opens up new possibilities for the manufacturing world.
Characteristic | Traditional Robots | Collaborative Robots | Adaptive/Intelligent Robots |
---|---|---|---|
Speed and Load Capacity | High | Low | Moderate |
Physical Barriers | Required | Not Required | Not Required |
Adaptability | Low | Moderate | High |
Robotics is always getting better, and we need new tech to make robots more flexible. By solving these problems, we can make robots work better in factories. This will help manufacturers use robots to their fullest potential.
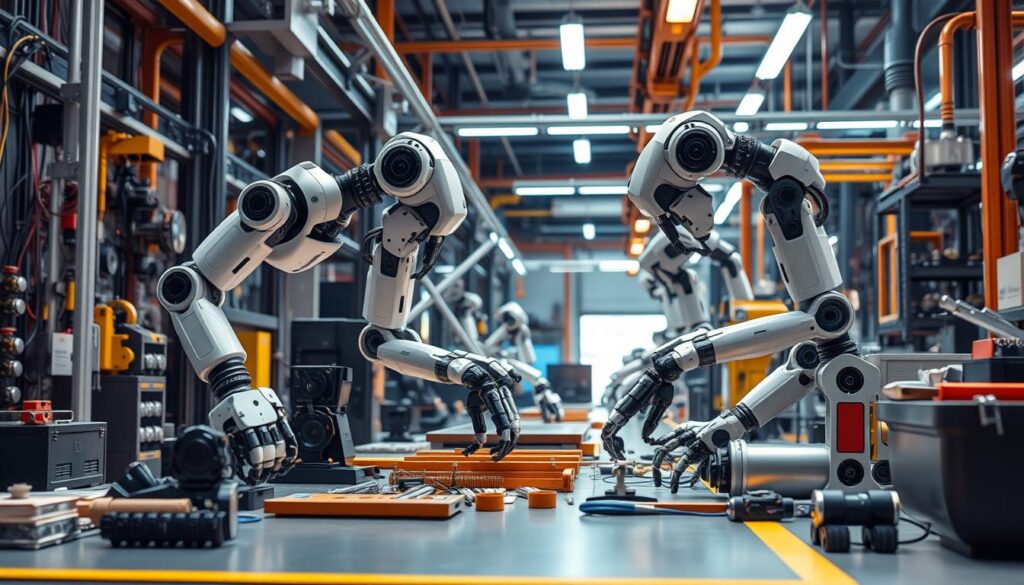
Workflow and Process Integration
Adding AI-driven robots to manufacturing workflows is a big challenge. It needs careful planning and checking. Companies must figure out how to use these new tools well. They aim for better productivity, efficiency, and teamwork between humans and robots.
One key part is looking at product workflows and how parts move to robots. Using data-driven process improvements helps find areas to get better. By looking at production data, companies can find and fix problems.
Seamless Integration for Optimal Productivity
For industrial robot workflow integration to work, a few steps are needed:
- Initiate Project Planning: Set goals, check risks, and plan the project.
- Conduct Factory Floor Analysis: Watch KPIs like production time and quality to boost productivity and cut costs.
- Design Automation Architecture: Use design tools, write scripts, and define roles for better human-robot collaboration.
- Select Industrial Robots or Machines: Pick equipment that fits the production line well.
- Develop Software Integration Plan: Find out what tech is needed to make things run smoothly and reduce manual work.
- Configure Industrial Robots or Machines: Work together to set up machines, calibrate sensors, and adjust settings for quality and efficiency.
- Implement Safety Protocols: Do risk checks and train to keep the workplace safe.
- Test and Validate System: Test thoroughly, including unit testing and UAT, to make sure the system works well.
- Train Personnel on New Systems: Create training to help employees use the system well.
- Continuously Monitor and Improve: Keep checking how things are going and get feedback to find and fix problems for better productivity.
By taking these steps, manufacturers can smoothly add AI-driven robots to their workflows. This leads to better productivity, efficiency, and teamwork between humans and robots.
Conclusion
Industrial robots bring big benefits like more efficiency and productivity. But, they also come with challenges. These include high costs, complex setup, tricky programming, and safety worries.
As tech gets better and rules change, solving these problems will get easier. This will help robots become even more important in making things.
Artificial intelligence in robots can change how we make things. It can make products better, cut down on mistakes, and make work faster. But, using these new tools right needs careful planning and training.
By tackling these issues, companies can use robots and AI to their fullest. This will help them stay ahead in the global market.
The need for smart robots in making things is only growing. The industry must keep up and find ways to use these tools well. This will help companies grow and succeed in the long run.
The future of making things looks bright. It will mix human skills with advanced automation. This will make work more efficient, productive, and green.