Industrial robots have changed how industries work, making them more efficient and precise. But, there are big challenges when adding these robots to the workplace. These include high costs, complex setup, and safety issues.
The growth in industrial robotics is fast, thanks to new automation tech. Manufacturers want to use collaborative robots (cobots) to improve production. But, adding these robots to current systems is hard and requires solving many technical and organizational problems.
Starting with robots costs a lot, and programming them is complex. Ensuring safety when humans and robots work together is also a big challenge. This article will look at these issues and offer solutions to help manufacturers stay ahead in the global market.
Initial Costs and Investment Barriers
Starting with industrial robotics and automation can be tough because of the high costs. Buying top-notch robots and the needed tools and software is expensive. This can stop smaller businesses or those with limited budgets from starting.
But, the long-term gains like making more products and saving on labor costs are worth it. These benefits can make the initial cost seem less daunting.
High Upfront Expenditure
The price of industrial robots has dropped from $63,000 in 2009 to $45,000 in 2018. This makes them more affordable. Yet, the cost of starting with robots is still a big hurdle for small and medium-sized businesses.
A study by Loup Ventures shows that global robotics spending could hit $13 billion by 2025. This shows that more people are interested in automation.
Securing Funding for Robotic Automation
Finding money for robots and programming can be hard. Many investors see it as a risky choice. They think the benefits won’t show up for a long time because setting up robots takes a lot of time.
But, as robots get cheaper and better, their value is clearer. This makes investing in robotic process automation (RPA) more appealing.
Integration and Technical Complexities
Adding industrial robotics development to current workflows is complex. Many industries have automation technologies already. They need to carefully plan to add robotic system integration without problems.
There are issues with making the robotic systems work with the old machinery. Also, people need special training to use these new systems. This makes it hard to integrate them.
Manufacturers face a big problem: there’s no global standard for programmable logic controllers or robotics. This makes setting up robots slow and hard. It also needs experts who know how to program them well.
The lack of a standard for industrial internet of things (IIoT) programming is another big challenge. It requires special skills to make sure these systems work well with what’s already there.
Key Challenges | Impact |
---|---|
Compatibility with Existing Systems | Requires careful planning and collaboration with robotics experts to integrate industrial robots into established production lines without disrupting operations. |
Lack of Standardization in Programming Languages | Increases complexity and time required for deployment, necessitating specialized programming skills to ensure successful integration. |
Getting past these technical hurdles is key for manufacturers. It’s especially important for small and medium-sized businesses. They need to use industrial robotics development and automation to grow and succeed.
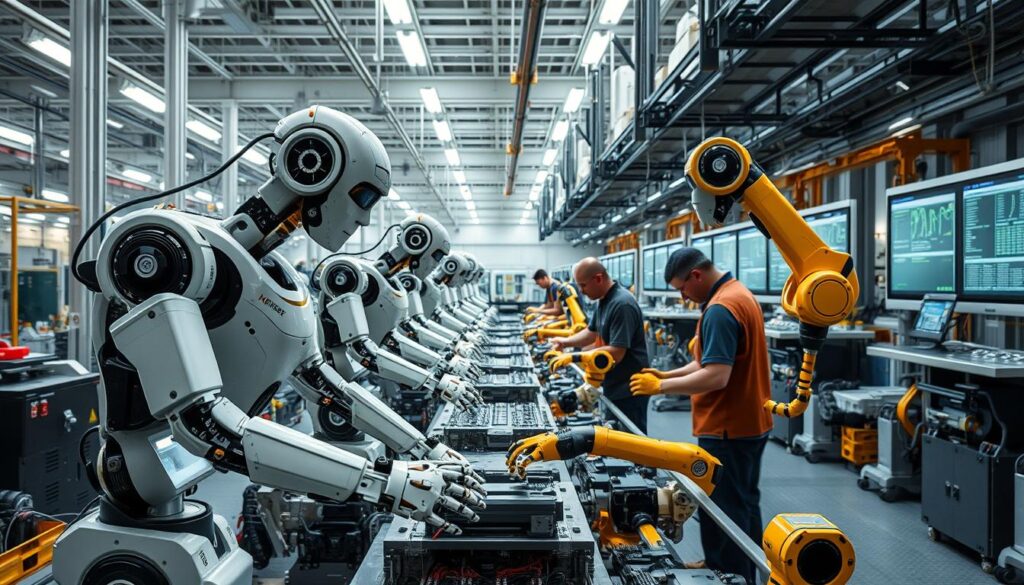
Industrial robotics development (cobots)
The world of industrial robots has changed a lot. This is thanks to the rise of collaborative robots, or “cobots.” These robots work with humans, making work better, safer, and more flexible in many places.
Cobots have special sensors and software. They can move safely with people around. They even stop if they might hit someone, keeping everyone safe. This is why more places want to use cobots.
Cobots are also very flexible. They can do many tasks, which is great for places that change a lot. They are also cheaper to start up, which helps more places use them. This is why cobots are becoming popular in many fields, like making things, moving goods, and in healthcare.
Key Cobot Advantages | Key Industrial Robot Advantages |
---|---|
|
|
Choosing between a cobot and a traditional robot depends on many things. It’s about the size of the job, how complex it is, and how safe it needs to be. But, cobots have really changed how we think about using robots in work. They help humans and machines work together better.
Programming Challenges and Skill Gaps
Creating advanced industrial robots, like collaborative robots (cobots), needs special programming skills. The complex programming languages and the need for precision are big challenges. These issues make it hard for industries to use automation efficiently and safely.
One big problem is the lack of skilled robotic programmers. Studies show that training workers in robotics can boost their productivity by over 70%. But, 83% of manufacturers struggle to find and keep good workers, a recent report found.
Complex Programming Languages
Traditional industrial robots are programmed less often because they do simple tasks. Cobots, however, need to be reprogrammed more for tasks that require customization. This shows the need for easier and more efficient ways to program them.
Old programming methods for industrial robots don’t work well for cobots. This is because cobots work together with humans and have different tasks. Programming cobots for small batches is often too expensive, making efficient programming crucial.
Shortage of Qualified Robotic Programmers
The lack of skilled workers is a big problem for manufacturers worldwide. A 2021 study by Deloitte and The Manufacturing Institute says there will be 2.1 million unfilled U.S. manufacturing jobs by 2030, costing the economy $1 trillion in 2030 GDP. The World Economic Forum also predicts a shortage of over 7 million skilled manufacturing workers globally by 2030.
This shortage of skilled programmers is a major challenge for industries wanting to use industrial robotics development and robotic process automation (RPA). To overcome this, targeted training and education programs are key. They will help industries adopt advanced automation technologies successfully.
Safety Considerations and Collaborative Workspace
As collaborative robots (cobots) become more common in factories, keeping humans safe is key. The use of robotics safety standards and industrial internet of things (IIoT) is crucial for a safe work area.
It’s important to have strong safety steps like sensors, emergency stops, and barriers. Also, training workers on how to safely use these robots is vital. This helps avoid accidents and injuries.
Cobots come with safety features like speed controls and force limits. These help them work safely with people nearby. This makes the workplace safer for everyone.
Safety Measure | Description |
---|---|
Speed and Separation Monitoring | Sensors detect workers and adjust the robot’s speed to keep a safe distance. |
Hand-Guided Controls | Allows manual control of the robot’s movements, enabling operators to guide the cobot’s actions directly. |
Power and Force Limiting | Reduces the robot’s force and torque to prevent potential harm to human operators. |
Safety-Rated Monitored Stop | Automatically stops the robot when a worker is detected in the collaborative workspace. |
Groups like the International Organization for Standardization (ISO) and the American National Standards Institute (ANSI) have set safety rules. Following these rules is essential for a safe work environment.
As collaborative robots become more popular, using advanced safety tech is crucial. Following robotics safety standards is key for a safe and productive industrial internet of things (IIoT) space.
Organizational Resistance and Change Management
The introduction of industrial robotics development and robotic process automation (RPA) in the workplace often faces resistance. Small and medium-sized enterprise (SME) manufacturers worry about losing jobs. They fear that automation will replace their workers.
Despite a labor shortage in manufacturing, workers still worry about job loss. A 2022 study found that only 14% of workers have seen their job replaced by a robot. It’s important to clearly explain the automation plans, including training and new tasks for workers.
Fear of Job Displacement
The use of industrial robotics development and robotic process automation (RPA) can change organizations. But, employees often fear losing their jobs. This fear comes from uncertainty and a desire to stay in their comfort zones.
Communication and Worker Involvement
To reduce job displacement fears, involve workers in the automation process. Explain the plans for industrial robotics development and robotic process automation (RPA). Offer training and upskilling opportunities to ease their worries.
This approach helps in a smooth transition. It ensures the successful use of robotic technologies in the workplace.
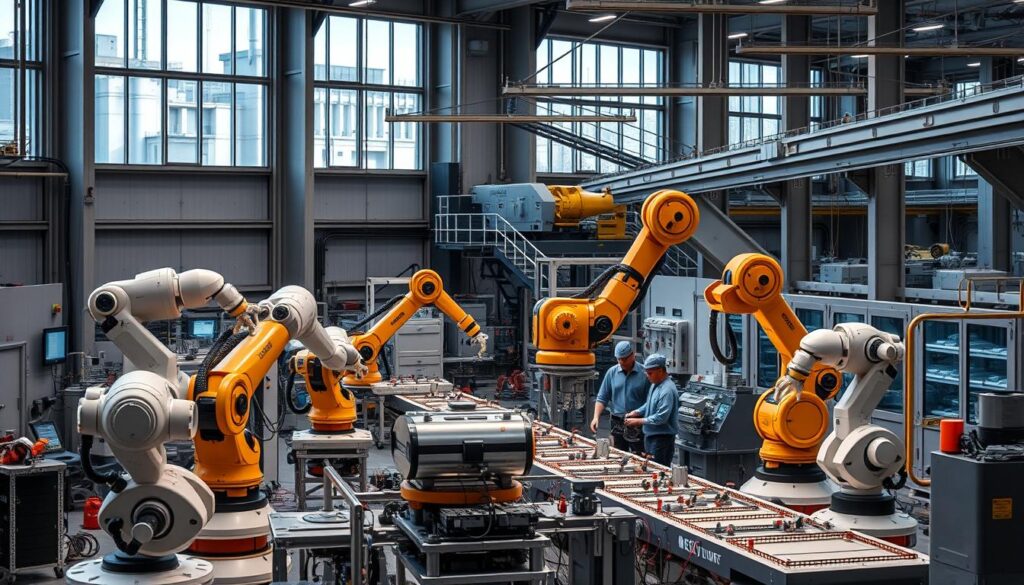
Conclusion
Industrial robotics and automation technologies are changing the game in many industries. They promise more efficiency and productivity. But, there are big hurdles to overcome, like high costs and safety issues.
Collaborative robots, or cobots, are making things easier for businesses of all sizes. They are safe and affordable, helping to bring automation to more places. Studies show that teams with humans and robots can work up to 85% faster.
As technology and standards improve, these challenges will get easier. By tackling issues like programming and safety, industries can unlock the full potential of automation. This will lead to a future where robots are even more crucial in shaping our work world.