In the world of industrial robotics, making robots faster and smoother is key. Developers use special motion profiles to do this. These profiles help robots move better and more efficiently.
Trapezoidal profiles let robots change speed quickly but can cause shakes. On the other hand, S-curve profiles keep the robot moving smoothly. This makes the robot more stable and reliable.
Developers adjust the S-curve profile to balance speed and smoothness. This is vital for tasks that need both speed and precision. It helps in making products better and keeps robots safe.
The use of advanced motion control is becoming more important. It helps in making robots work better and faster. This is thanks to the industrial internet of things (IIoT) and robotic process automation (RPA).
Understanding Motion Profiles
In the world of industrial robotics, making robotic movements faster and smoother is key. Two main types, trapezoidal and S-curve, have their own strengths and weaknesses. They help control how robots move.
Trapezoidal vs. S-Curve Motion Profiles
Trapezoidal profiles have three parts: speeding up, coasting, and slowing down. It’s easy to set up but can cause big vibrations. On the other hand, S-curve profiles have seven parts, making the motion smoother.
S-curve profiles are great at reducing vibrations and shaking. They keep the acceleration smooth, unlike trapezoidal profiles. Adjusting the phases can make the motion faster or smoother, depending on what’s needed.
Motion Profile | Phases | Vibration Reduction | Transfer Time |
---|---|---|---|
Trapezoidal | 3 (Accelerate, Coast, Decelerate) | Lower | Faster |
S-Curve | 7 (Acceleration Transition, Acceleration, Acceleration Transition, Deceleration Transition, Deceleration, Deceleration Transition, Coast) | Higher | Slower |
Choosing between trapezoidal and S-curve depends on what the task needs. It’s about finding the right balance between speed, smoothness, and stability.
Industrial Robotics Development
In the era of Industry 4.0, industrial robotics are key in modern smart factories. They handle tasks like material handling and quality inspection. But, traditional robot controllers are not flexible enough for changing needs.
Developers are now working on new control and programming solutions. They aim to create flexible, modular, and open architectures. This will make robots easier to integrate into different plants.
The Unimate robotic arm’s introduction in the 1960s started the industrial robotics industry. It led to robots being widely used in manufacturing. Today, robots are more efficient thanks to artificial intelligence (AI).
The industrial internet of things (IIoT) and robotic process automation (RPA) are changing manufacturing. The need for automation engineering and robotic system integration is growing. Developers are making smart, connected robots that can adapt to industry needs.
Key Developments in Industrial Robotics | Impact |
---|---|
Introduction of the Delta robot in the 1980s | Improved efficiency in picking and packing tasks due to high speed and precision |
Increased usage of advanced sensors in the 1990s and 2000s | Enhanced robotic arms’ accuracy and flexibility in industrial manufacturing |
Development of Collaborative robots (Cobots) | Allowed for safe and efficient human-robot collaboration in manufacturing |
Integration of artificial intelligence (AI) in industrial robots | Enabled robots to learn and adapt, increasing their efficiency |
As the industry evolves, industrial robotics development will be more important. It will help drive productivity, efficiency, and innovation in manufacturing.
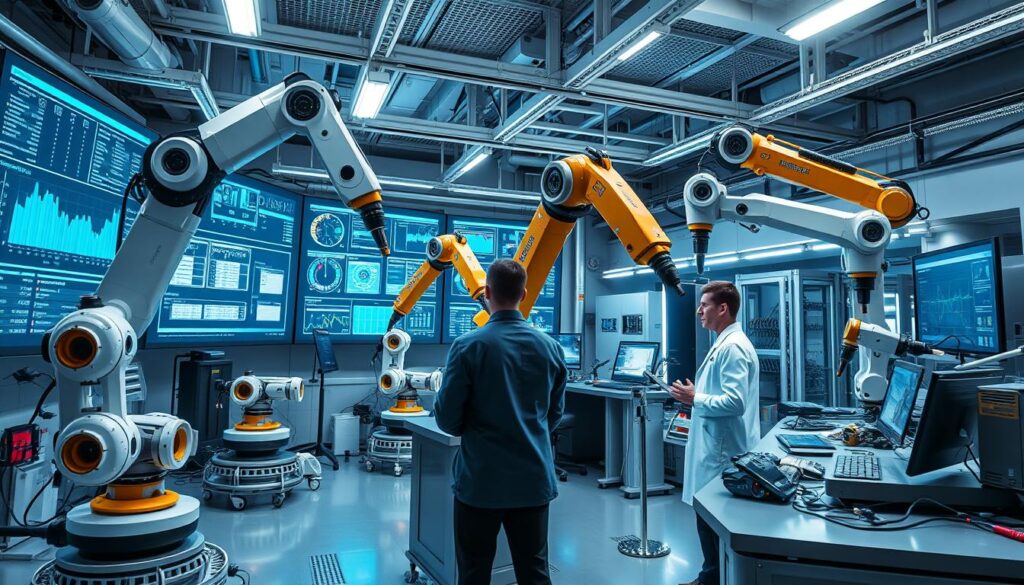
Trajectory Following and Motion Queues
Trajectory following is key in industrial robot control. It aims for the robot’s path to closely match the planned path. This needs teamwork between the designer and the control engineer to avoid errors.
Many robot controllers have motion queue features. This lets users set up a series of motions or waypoints. The controller then makes a smooth path for the robot to follow.
Interpolation Profiles and Motion Generation
Articulated robot control is all about teamwork. It’s about making sure the robot moves right without hitting anything. This is especially true in tight spots where speed matters.
Motor controllers are vital for robots. They turn digital signals into motor commands. They handle things like speed control and fault detection.
Multi-axis controllers add cool features like Cartesian control and synchronized movements. These help robots move better and more smoothly. Smooth paths are key to avoid mistakes and overheating.
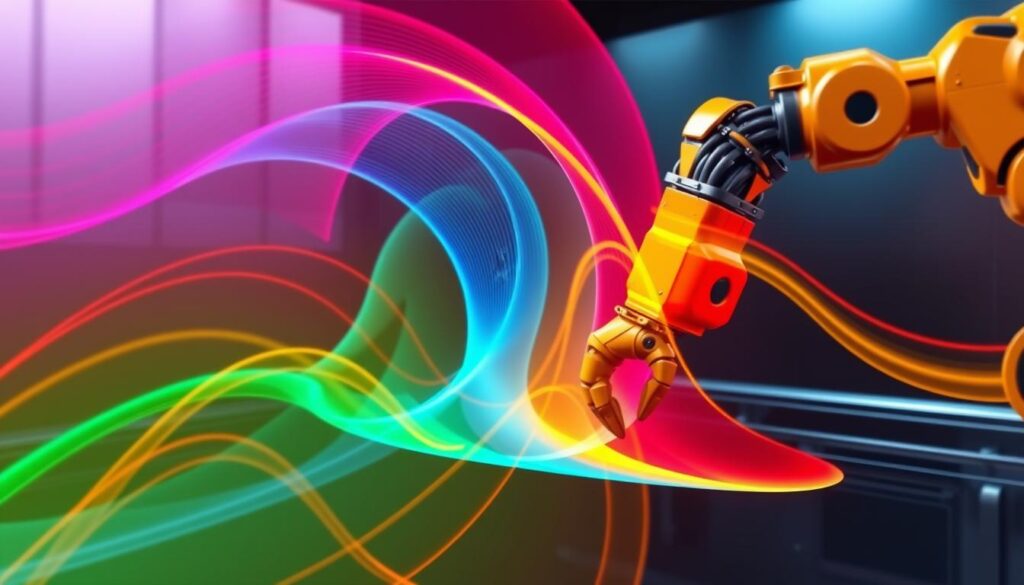
Robots use PID controllers to stick to their paths. Motor controllers help with this by using motion queues. This makes it easier for designers and keeps the robot moving smoothly.
There are different types of interpolation profiles. They help meet the robot’s movement needs. The right profile can make the robot move better and follow its path more accurately.
Challenges in Industrial Robot Control Systems
Traditional industrial robot control systems face many challenges. They are not very flexible or adaptable in today’s smart factories. The closed architecture and proprietary programming languages make updates hard. It’s tough to add new features based on changing production needs.
The lack of interoperability between robots from different makers is another big problem. It makes it hard to create systems where robots work together smoothly.
Also, robots can’t easily talk to other devices like sensors and actuators. This limits how well production system parts can work together. The complex control applications needed for advanced robots add to these problems. They require special skills and knowledge.
To solve these issues, there’s a growing focus on smart industrial robot control methods. These methods aim to make programming easier and less prone to errors. They focus on cognitive robotics, which can adapt to changing production needs and offer more flexibility.
Key Challenge | Impact | Solution |
---|---|---|
Closed architecture and proprietary languages | Difficulty in maintaining, updating, or adding new functionalities | Adoption of open-source and standardized control systems |
Lack of interoperability between robots | Complications in developing coordinated multi-robot control systems | Improved communication protocols and integrated control platforms |
Restricted integration and communication with external devices | Challenges in dynamic collaboration within smart factories | Increased connectivity and data integration across the production system |
Complex control applications | Specialized expertise and skills required for advanced industrial robotics | Advancements in cognitive robotics and dynamic adaptation capabilities |
As the industrial robot market grows, solving these challenges is key. It will unlock the full potential of industrial robot control systems in Industry 4.0 and the evolving smart manufacturing world.
Conclusion
Developers are key in making industrial robots faster and more efficient. They use advanced motion profiles like S-curves. This makes the robots move smoothly and quickly, reducing shaking and wobbling.
But, traditional robot control systems are closed and hard to change. This makes it tough to adapt and work together with other systems. Researchers are working on new, open systems that can handle the needs of Industry 4.0.
As more robots are used, developers must focus on speed, security, and working together. This will help robots fit well into smart factories. It will make factories more efficient and competitive worldwide.