Adding industrial robotics development to factories can boost productivity and efficiency. But, safety must always be the top priority for human-robot collaboration. Developers need to set up strong safety measures, find and fix risks, and train workers well. They also need to create barriers and controls for safe human and robotic automation systems interaction.
As industrial robot programming and robot kinematics and dynamics get better, so does the need for a solid safety plan. This includes using robot vision and sensing tech and robot control architectures that keep humans safe. By focusing on safety, developers can fully use industrial robotics simulation and robotic cell integration. This ensures a safe space for human-robot interaction.
The success of industrial robotics development depends on a detailed safety plan. This plan should cover design, maintenance, and monitoring. By setting up strong safety measures, finding and fixing risks, and training workers, developers can make a safe space. Here, humans and robots can work together, driving innovation and keeping everyone safe.
Comprehensive Safety Protocols for Industrial Robot Safety
Adding industrial robots to your factory can boost efficiency and productivity. But safety must always come first. It’s vital to follow strict safety rules to protect workers and keep the workplace safe. Let’s look at the main parts of a strong safety plan for industrial robots.
Get the Installation Right
Safe robot use starts with correct installation. Work with skilled experts who follow the safety guidelines from the robot maker. Small mistakes during setup can lead to many accidents.
Restrict Access
Use physical barriers like cages or fences around robot areas. Add light curtains or sensors that stop the robot if someone gets too close. Keeping people away from robots is key to safety.
Train, Train, Train
Everyone near robots needs safety training. Teach your team about safety steps, how to stop the robot in an emergency, and how to spot dangers. Keep training up to date to keep safety a priority.
Regular Maintenance is Your Friend
Stick to the robot maker’s maintenance schedule. Well-maintained robots are less likely to break down and cause accidents. Regular checks can greatly lower the risks of robot use.
Plan for the Unexpected
Make detailed emergency plans and make sure everyone knows what to do in an accident. Being ready for surprises can help lessen the effects of any robot-related incidents.
By focusing on these safety steps, you can use industrial robots safely. This protects your team and keeps your work area safe and productive. Investing in safety is crucial for your factory’s success.
Identifying and Mitigating Risks
Adding industrial robots to the workplace needs careful risk checking. First, look at the work area, pick the right robot, and set up safe zones. Doing a full risk check and focusing on safety training helps avoid dangers in working with robots.
Assess the Work Environment
Begin by checking the work area for dangers. Think about the robot’s space, human paths, and any things that could get in its way. Look for spots where the robot might hit people or things nearby.
Choose the Right Robot
Pick a robot made for your job, focusing on ones with safety features. Look for ones with sensors, stop buttons, and barriers to lower crash risks.
Establish Safety Zones
Make special robot areas with barriers, signs, and extra sensors. These zones keep people safe and stop robots and people from getting too close.
Conduct a Comprehensive Risk Assessment
Look at all possible dangers, how bad they are, and how likely they are to happen. Then, suggest ways to fix these risks, like special tools, rules, and safety gear.
Prioritize Safety Training
- Give all workers safety training before robots arrive.
- Teach them how to safely work with robots, what areas are off-limits, and what to do in emergencies.
- Make sure they know how crucial it is to follow safety rules and help keep the workplace safe.
By doing these things, employers can make a strong safety plan. This protects their workers and helps robots work better together with people.
Implementing a Comprehensive Industrial Robot Safety Training Program
Keeping workers safe in an industrial robotics setting is crucial. A detailed training program is key. It should cover industrial robot programming, robot safety standards, and simulation.
First, figure out who needs training. This includes robot operators, technicians, maintenance staff, supervisors, and anyone near robots. The training level will depend on their role.
- Do a thorough risk assessment to find potential hazards. This includes routine and non-routine risks, like during maintenance or setup.
- Create a customized curriculum. It should include both basic safety principles and specific steps, like lockout/tagout.
- Use different training methods. Include presentations, hands-on demos, and videos to help everyone learn well.
But, training once isn’t enough. You need regular refreshers, drills, and retraining. This keeps lessons fresh, updates teams, and fills knowledge gaps. Safety training should always be ongoing.
With a thorough safety training program, your team will be well-informed. They’ll know the risks and have the skills to work safely with industrial robots.
Implementing Effective Safety Barriers and Controls
Keeping industrial robotics safe is key. This means setting up strong safety barriers and controls. Robots need many safety features to protect people from harm. These include physical barriers, safety mats, emergency stops, and safe programming.
Physical Barriers
Physical barriers like fences and doors keep humans away from robots. They stop people from getting too close. Light curtains also work by using infrared beams to stop the robot if someone gets too close.
Safety Mats
Safety mats around the robot are very important. They stop the robot if someone steps into the area. This helps prevent accidents and injuries.
E-stops
Emergency stop buttons, or E-stops, are a quick way to stop the robot. They should be easy to find and use. When pressed, the robot stops right away.
Programming
Safe programming is also vital. Programmers set limits on the robot’s actions to prevent harm. They do a safety check to find and fix any risks.
With these safety measures, robots can work safely with people. This makes sure everyone is protected. It also follows important safety rules like ANSI/RIA R15.06-2012 and ISO 10218.
Regular Maintenance and Safety Checks
In the world of robotics development, keeping things running smoothly is key. Regular checks help avoid big problems before they start. This keeps your robot safety standards high and your production running smoothly.
Stick to the robot maker’s maintenance schedule. This means following their rules for when to check, oil, replace parts, and calibrate. It’s also important to test safety systems and make sure sensors and barriers work right.
Keep a record of every maintenance task. Write down what you did, any issues found, parts swapped, and software updates. These records are crucial for safety checks and audits. Always know the latest safety rules and update your maintenance and safety plans as needed.
Regular maintenance and safety checks are vital. They make your robots reliable, boost productivity, cut downtime, and protect your workers.
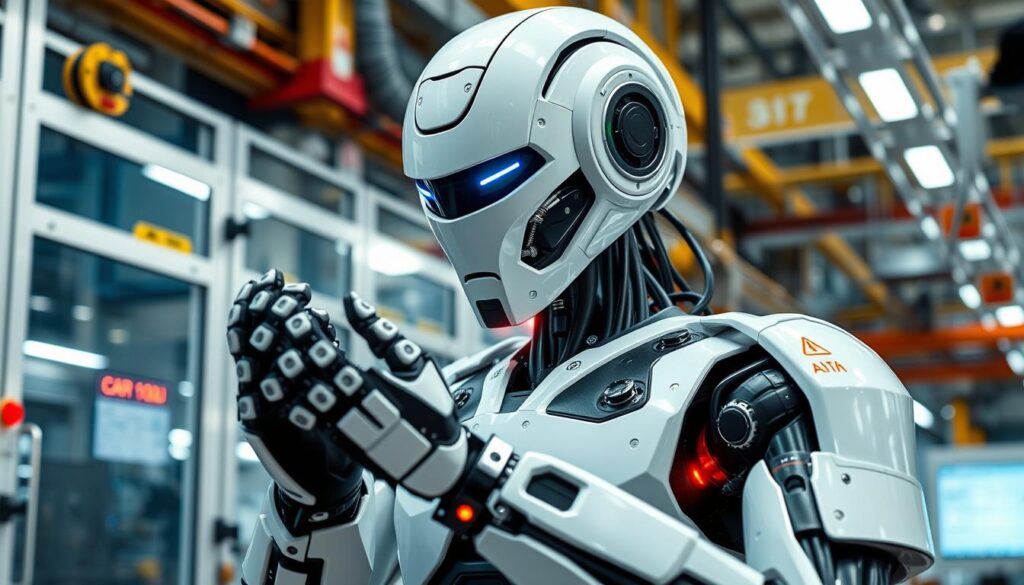
Safety in Collaborative Robot Applications
Collaborative robots, or cobots, are becoming more common in many industries. It’s vital to ensure they work safely with humans. Knowing the right safety steps is key to avoiding accidents.
Understanding where a cobot can safely interact with humans is important. Before working near a cobot, learn its safe zones. Staying within these zones helps keep everyone safe.
Mindfulness of the cobot’s operating speed is also crucial. Even at slower speeds, cobots can still cause harm. Being alert and moving carefully can reduce risks.
Cobots use sensors to detect humans and stop safely. But, it’s crucial to stay aware of your surroundings. Avoid sudden moves that might confuse the sensors. Knowing how to react during a safety stop is also important.
Even with safety features, a detailed risk assessment is needed. This helps find and fix potential dangers. It ensures everyone’s safety when working with cobots.
The robotics field is growing, with new safety features and standards emerging. By following safety guidelines, companies can use cobots safely. This benefits both the technology and the people working with it.
Industrial robotics development
The future of industrial robotics is changing. Humans and machines will work together more. This change makes safety a big concern. It’s important to make sure humans and robots can work safely together.
Robots need to follow strict safety rules. This includes ISO and industry standards. It also means the robot can work with people without problems.
Research on safety in human-robot interaction is ongoing. This research helps make robots safe for people to work with. It’s all about creating a safe and smooth interaction between humans and robots.
Key Developments in Industrial Robotics | Percentage Growth |
---|---|
Global industrial robots in operation | 10% increase in 2021 |
Sales of new industrial robots | 0.5% growth in 2020 |
Industrial robotics market size | 9.3% CAGR from 2020 to 2026 |
Collaborative robot (cobot) market | 32.5% CAGR projected from 2021 to 2030 |
Global robotics Venture Capital (VC) investment | 38% year-on-year growth in 2021 |
The field of industrial robotics is growing fast. Advances in robot kinematics and dynamics, robot vision and sensing, and robot control architectures are key. These improvements are making robotic automation systems better. They are changing industries like automotive and mining.
As the industry grows, safety, sustainability, and easy use are key. These areas are at the heart of industrial robotics development.
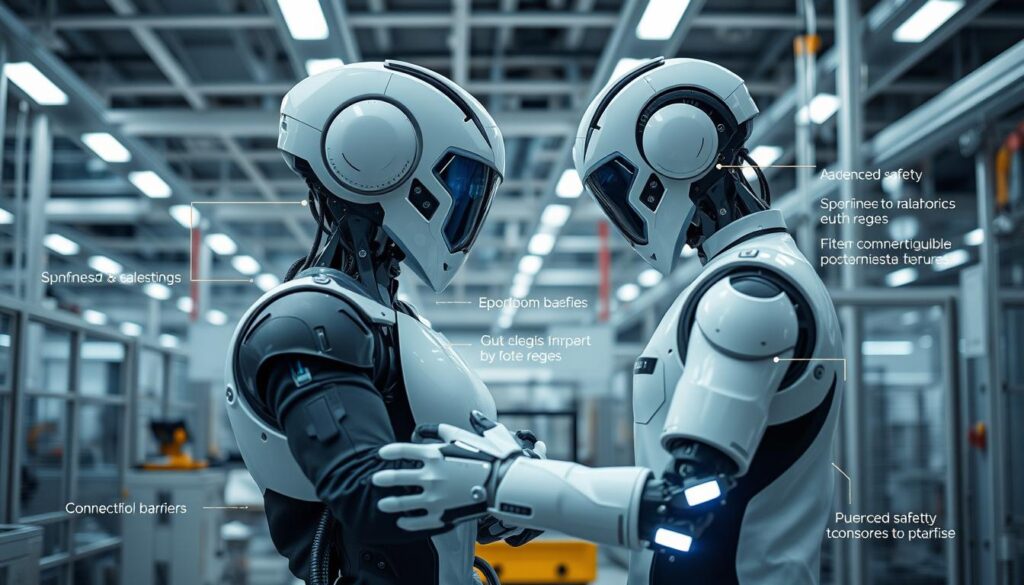
Conclusion
Industrial robotics has changed the way we make things, making it faster, more precise, and safer. By setting up strict safety rules, finding and fixing risks, and training workers well, we’ve made it safe for humans and robots to work together. This has opened up new possibilities in the factory floor.
Robots now use smart sensors, AI, and teamwork to do complex jobs better than ever. As we move towards Industry 5.0, we’ll see even more improvements. AI and IoT will make factories work even more efficiently.
But, using robots in factories isn’t easy. There are costs, fitting them into old systems, and training workers. Yet, by focusing on safety, following rules, and keeping safety up to date, companies can overcome these hurdles. This way, they can fully benefit from the latest in automation.