Vibration is a key but often overlooked issue in making industrial robots. Companies want to use robots to save money and replace expensive human labor. They look at how much money they can save and how long the robot will last.
Developers and engineers must think about the robot’s performance and its parts. For example, the reducer can cause vibrations that affect the robot’s accuracy and lifespan.
Today’s industrial robots are a mix of being stiff and light. They use artificial intelligence and automation systems. But, compared to older robots, they can vibrate a lot during fast movements. This makes it hard to keep the robot moving quickly and accurately.
It’s important to reduce vibration and noise in industrial robots. This ensures the robots are reliable, safe, and easy to use. Developers need to design flexible parts, choose the right materials, and use techniques to stop vibrations. This helps solve the problems robots face in their work.
Vibration: An Overlooked Challenge in Robotics Design
In the world of industrial robotics, managing vibration and noise is a big challenge. As systems get more advanced, with better robotic manipulation and artificial intelligence, vibration becomes a bigger problem.
The Compromise Between Rigidity and Lightweight
Designers of industrial robots have to balance between being rigid and light. Precision ball cycloidal reducers are great for lightweight robots in tasks like assembly and surgery. But, they can cause more vibrations because they’re not as stiff.
Collaborative Robots and Vibration Issues
The rise of collaborative robots brings new challenges. These robots are designed to work with humans and are lighter and more flexible. This flexibility can make them vibrate more during fast movements, affecting their precision.
Researchers are working on solutions, like the Multi-Mode FD-TVIST technology. It aims to reduce vibrations in these robots by improving their control.
Dealing with vibration in industrial robotics is key for accuracy and safety. It’s important for tasks like assembly and dangerous operations. To improve, we need better materials, control systems, and ways to dampen vibrations.
Researchers Seek Ways to Reduce Vibrations
As robotics in industry gets better, scientists are working hard to lessen vibrations. Vibrations can hurt the accuracy and speed of robots. This is especially true in tasks that use machine vision and artificial intelligence.
Flexible Joints and Links as Vibration Sources
Flexible parts of robots are a big problem. They help robots move but also cause unwanted shakes. Scientists are trying to find the right mix of stiffness for precision and lightness for speed.
Input Shaping Methods for Vibration Suppression
Scientists are looking into input shaping to reduce shakes. This method tries to cancel out shakes in light robots. But, it’s not perfect for shakes caused by outside forces. They’re also checking out new ways to cut down shakes in robots.
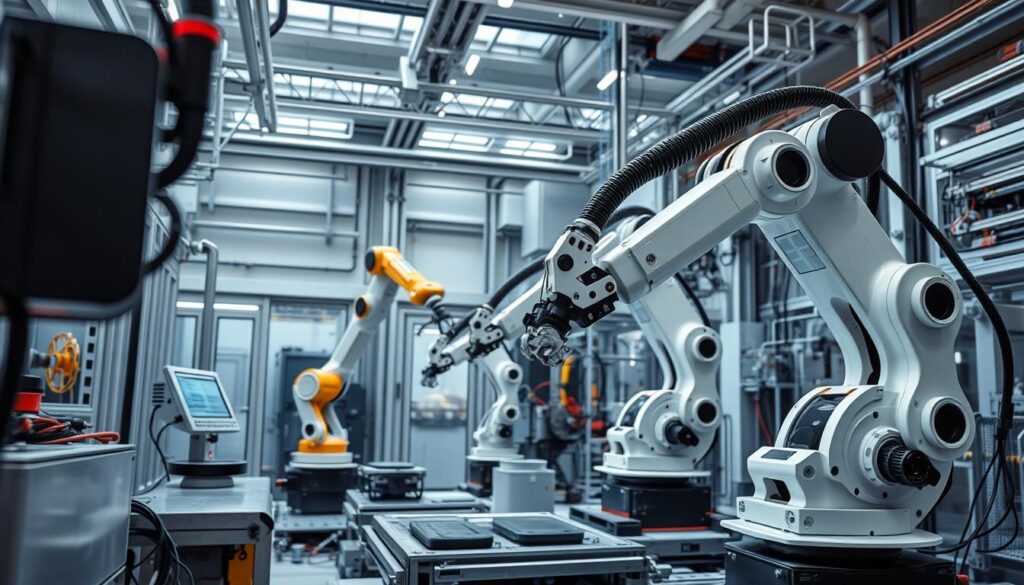
New tech in robotics and automation is making it more important to stop shakes. As robots work together in complex tasks, stopping shakes becomes a bigger challenge. This means we need better ways to handle shakes.
Vibration Reduction Technique | Effectiveness | Limitations |
---|---|---|
Input Shaping | Effective for residual vibration suppression in lightweight robot manipulators | Does not address vibrations from external disturbances |
Joint-space, Multi-Mode FD-TVIST | Demonstrated improved vibration reduction in industrial robotics applications | Requires advanced control algorithms and implementation |
As scientists keep looking for new answers, the future of robotics looks bright. We can expect robots to work even better and faster. They will be able to work well with advanced tech like machine vision and artificial intelligence.
Precision Ball Cycloidal Reducer: A Solution for Vibration Reduction
In the world of industrial robotics development, cutting down on vibration is key. The precision ball cycloidal reducer is a new approach to this problem. It’s a gearbox that replaces old strain-wave gears, offering better accuracy and less vibration.
This gearbox has a special design that makes it very precise. It’s also very stiff and lasts longer than other gearboxes. This makes it great for lightweight robotics like assembly and surgery.
The reason it reduces vibration is its design. The second cycloid movement has a different frequency than the first. This stops the system from vibrating. If the frequencies were the same, it would vibrate too much.
The cycloidal mechanism is also very durable. It’s almost impossible to destroy and will never wear out. This makes it a top choice for automation systems and robotic manipulation where vibration is a big problem.
The precision ball cycloidal reducer is a game-changer in industrial robotics development. It’s a reliable and innovative way to tackle vibration in machine vision, artificial intelligence, and more. It’s perfect for system integration in many areas.
Industrial robotics development: Advances in Noise Reduction
Industrial robots are becoming more common in our workplaces. The sounds they make can be distracting and affect our work. Luckily, new advancements are making robots quieter.
Designing Sounds for Robot-Human Interaction
The gender of a robot can impact how we see it. Researchers are working on voices and sounds that are neutral. They test these sounds to find the best way for humans and robots to interact.
Robots might even ask us what name we prefer. This way, they can match our preferences for a better interaction.
Robot Gender and Voice Considerations
Developers are also making robot sounds more natural. They aim to make robots sound like they’re part of the team. This is key for robots that work alongside us.
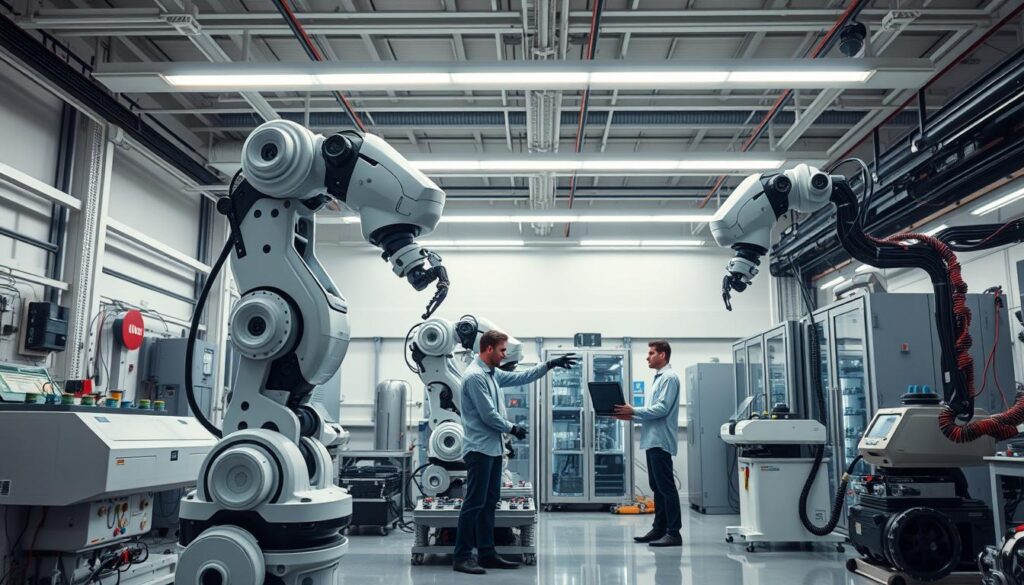
Noise reduction and sound design are crucial in robotics. By focusing on these, developers can make robots more comfortable and productive. This will help robots become a bigger part of our work lives.
Acoustic Design for Safety and User Experience
In the world of industrial robotics, sound design is key. It makes systems safer and easier to use. By adding sound cues, engineers make robots more natural to interact with.
Doppler Effect for Proximity Awareness
The Doppler effect is a smart way to alert people of a robot’s approach. As the robot moves closer, the sound changes pitch and volume. This helps users know when the robot is coming, making interactions safer and smoother.
Active Noise Cancellation and Sound Enhancement
Advanced sound tech like active noise cancellation is also used. It cancels out the robot’s noise, making it work better. Piezo loudspeakers add sounds that boost user confidence in the robot’s abilities.
By focusing on sound, robotics developers make systems safer and more user-friendly. This leads to better teamwork between humans and machines.
Standards and Compliance in Robotics
As robotics in industry keep getting better, it’s key to know the safety rules and compliance needs. These rules cover many areas, like mechanical and electrical safety, and how robots affect people and the environment. Robot makers and developers face a lot of rules and tests to make sure their robots are safe worldwide.
Hazards in Robotics
Robots can pose many dangers, like mechanical, electrical, and ergonomic risks. They can also cause thermal, noise, vibration, radiation, and material hazards. It’s important to find and fix these risks to make robots safe and responsible.
Testing Options for Robotics
There are many ways to check if robots are safe and work well. These include:
- Hazardous locations assessments
- Functional safety evaluation
- Process evaluations
- Mechanical safety testing
- Electrical safety testing
- Performance testing
- Environmental testing
- EMC & EMI testing
- Wireless and cybersecurity testing
These tests make sure robots follow global safety standards. This leads to safer and more reliable robots in industry and machine vision.
Global Standards and Regulations for Industrial Robots
As the world of industrial robots grows, rules and standards are key. They make sure these advanced systems are safe and work well. In the European Union (EU), robots follow certain rules. North America has its own set of guidelines.
European Union Standards
In the EU, robots are covered by the Machinery Directive and the Electromagnetic Compatibility (EMC) Directive. Makers must stick to EN and ISO standards. This includes EN 12100, ISO 13849-1, and others.
North American Standards
In North America, robots follow standards like ANSI/RIA R15.06 and ANSI/RIA R15.08. There’s also ANSI/UL 1740 and CAN/CSA Z434. These, along with ISO 10218-1 and ISO 10218-2, guide robot design and use in the U.S. and Canada.
Region | Key Standards |
---|---|
European Union |
|
North America |
|
These global rules help make sure robots are safe and reliable. They help the growth of industrial robotics development and automation systems in many industries.
Conclusion
The journey of industrial robotics has been amazing, with big steps forward in solving problems like vibration and noise. Researchers have found new ways, like using precision ball cycloidal reducers, to cut down vibrations. They’ve also worked on making sounds that are safe and better for users.
Now, industrial robots are everywhere in automation and more. It’s key to follow global rules to make sure these robots are used safely and well. The industry has grown a lot, from Industry 2.0 to Industry 4.0. This growth has brought in new robots that work together and move on their own, changing how we make things.
The future of Industrial Robotics looks bright, with new tech like artificial intelligence and smart motors leading the way. As we move forward, finding the right mix between humans and robots is important. It’s also key to think about jobs and how to make sure everyone is treated fairly.